- Overview
- Product Description
- Installation Instructions
- Certifications
- Packaging & Shipping
- Company Profile
- Our Advantages
- FAQ
Basic Info.
Product Description
This equipment is a new type of uncoiling, leveling, servo-feeding integrated machine specially designed for steel sheets with high yield strength in stamping. The friction between the material and the roller ensures that the servo feeding process will not slip to achieve high feeding accuracy.
The outlet is equipped with a new electronic automatic oiling device. The oiling roller is a soft rubber structure, which maximizes the even application of the oiled layer on the surface of the material and effectively protects the service life of the mold.
The equipment adopts a Japanese servo system, pneumatic components, bearings, and electrical components, and the control system adopts a large-size touch screen, which has a large-capacity user product parameter information memory function, and a complete equipment failure alarm system, which makes the automatic feeding equipment longer service life and work. Higher efficiency and more reliable safety factor.
Number | Name | Brand | ||
1 | servo motor | Yaskawa | ||
2 | 7-inch human-machine interface | Mitsubishi | ||
3 | 4.3 inch human-machine interface | Mitsubishi | ||
4 | Conventional motor | Taiwan TECO | ||
5 | Frequency converter |
| ||
6 | Pneumatic Components | SMC | ||
7 | PLC | Mitsubishi | ||
8 | Relay components, etc. | Schneider
| ||
9 | power cable | Baosheng cable(Flame retardant) |
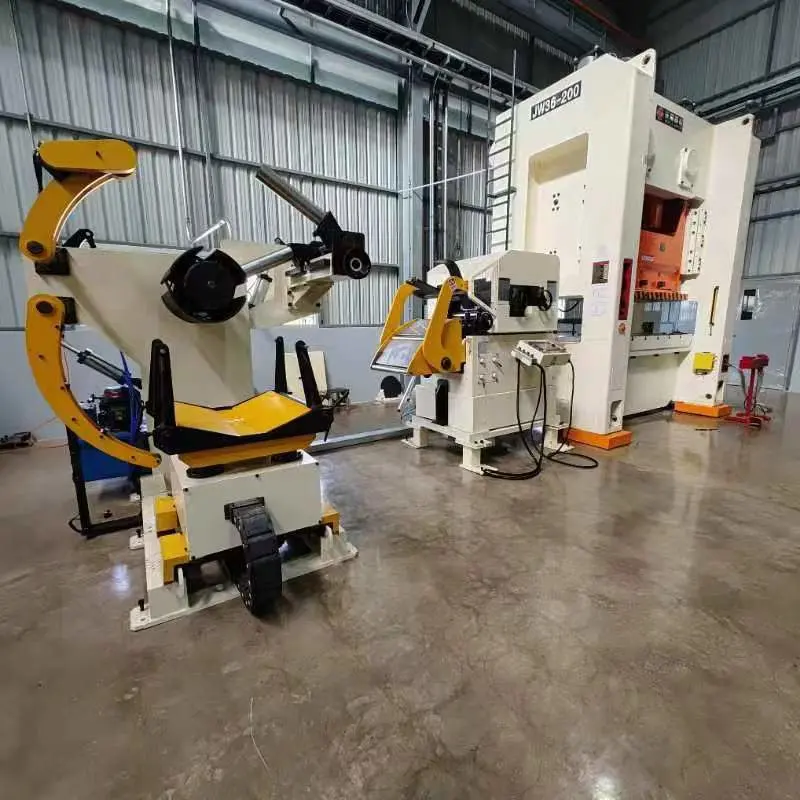
1. NC Servo feeding. Operating with Computerized Numerical Control by PLC program from MITSUBISHI made in Japan.
The electrical parts from YASKAWA are made in Japan including the Servo motor, driver, encoder, interface screen, and so on.
2. High precision feeding: to meet the coming of hi-tech industry, controlled by computer closed circuit feedback system to keep precision degree within +/-0.15mm
3. Feeding function: input 20 sets of different feed lengths, each group provides 999 times for punching or cutting to satisfy the processing of special products.
4. High-efficiency release device, match with adjustment of signal from the cutter or press machine through a cable wire.
5. Setting of feed length: directly input feed length on the control plate, and then it can reach the needed distance, feed length max 9999.99mm. speed max 100m/min
II. Straightening feature
1.3 in 1 uncoiler and straightener saves space and increases productivity.
2. Straightener and thickness adjustment by 4 worm gear micro-adjuster with reading 0.1mm advance reference indicator.
3. Feed and straightener roll with a hard chrome plate.
4. High rigid mechanical design sturdy construction, and high power output to secure proper straightening and feeding during the speed-increasing efficiency.
5. Electric loop control system.
6. Power hold down arm device
7. Inverse curve roll, easy to set up the curve up or down of feeding exit direction.
8. Feeding line is easily adjusted by an advanced worm gear screw Jacks device
9. Coil Material Entry support Assembly can bring the material into pinch rollers Automatically to save manpower and increase safety,
10. Coil side guide
11. Outgoing catenary to assist and support the material
12. A Cluster gear set maximizes the transmission of horsepower.
13. Transformer
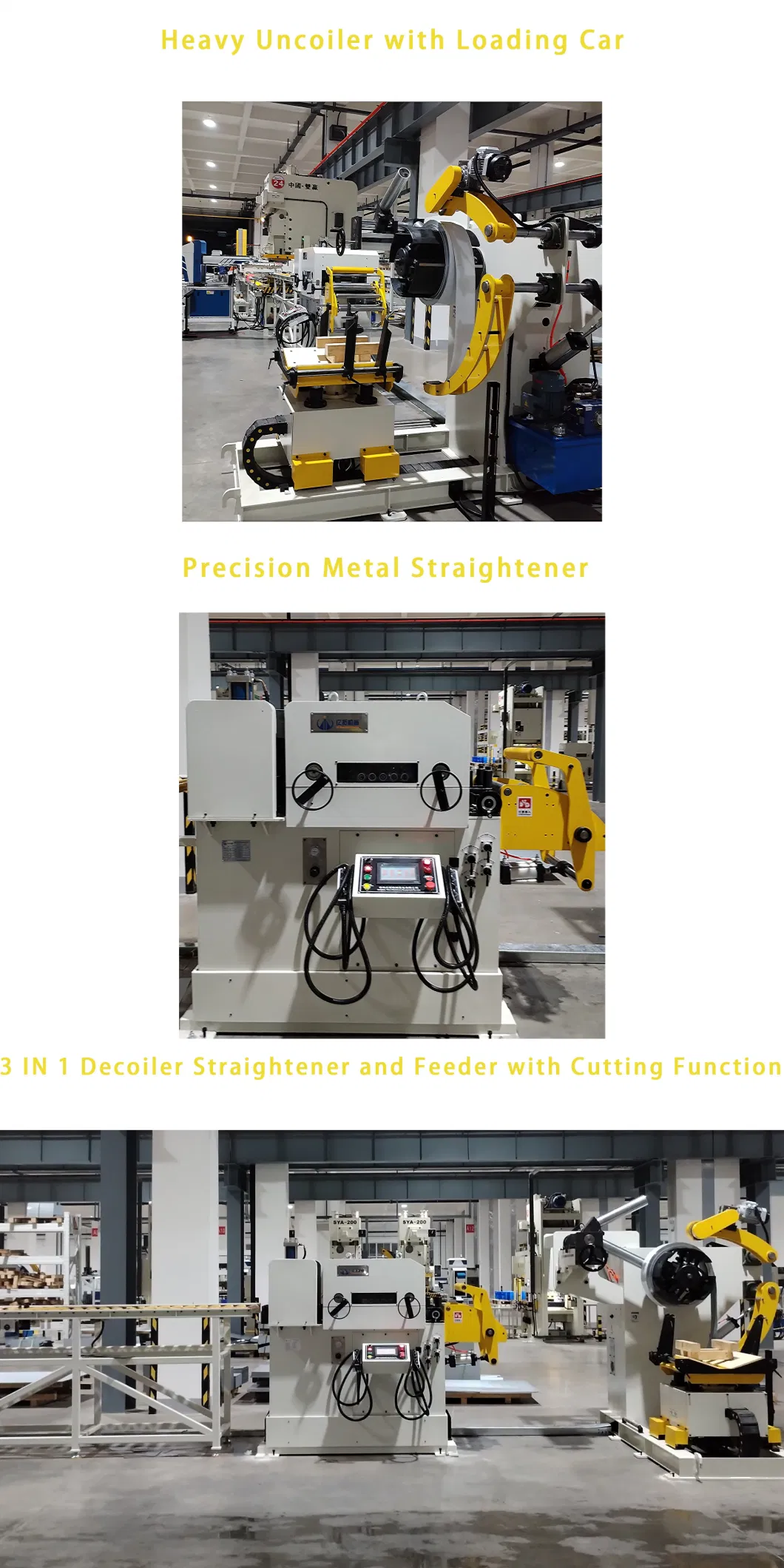
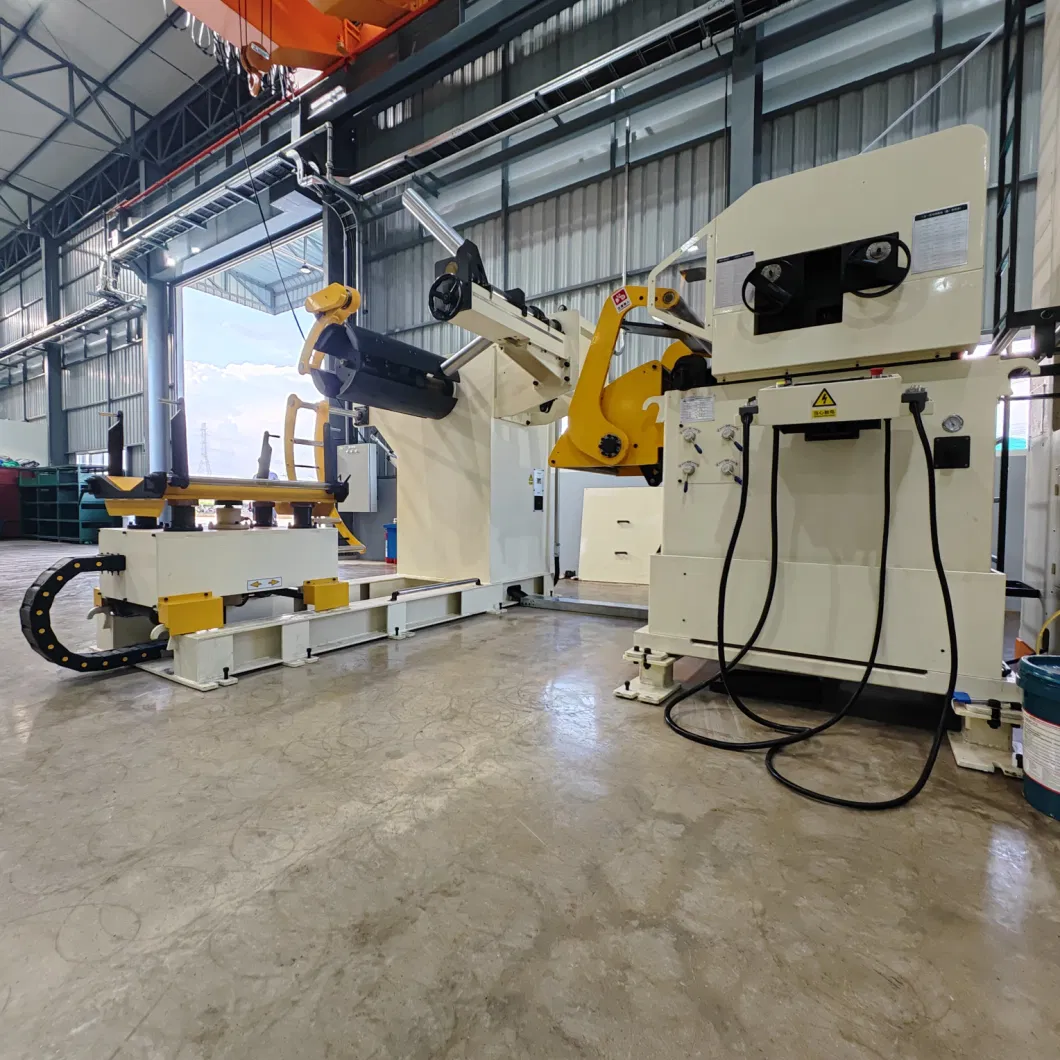
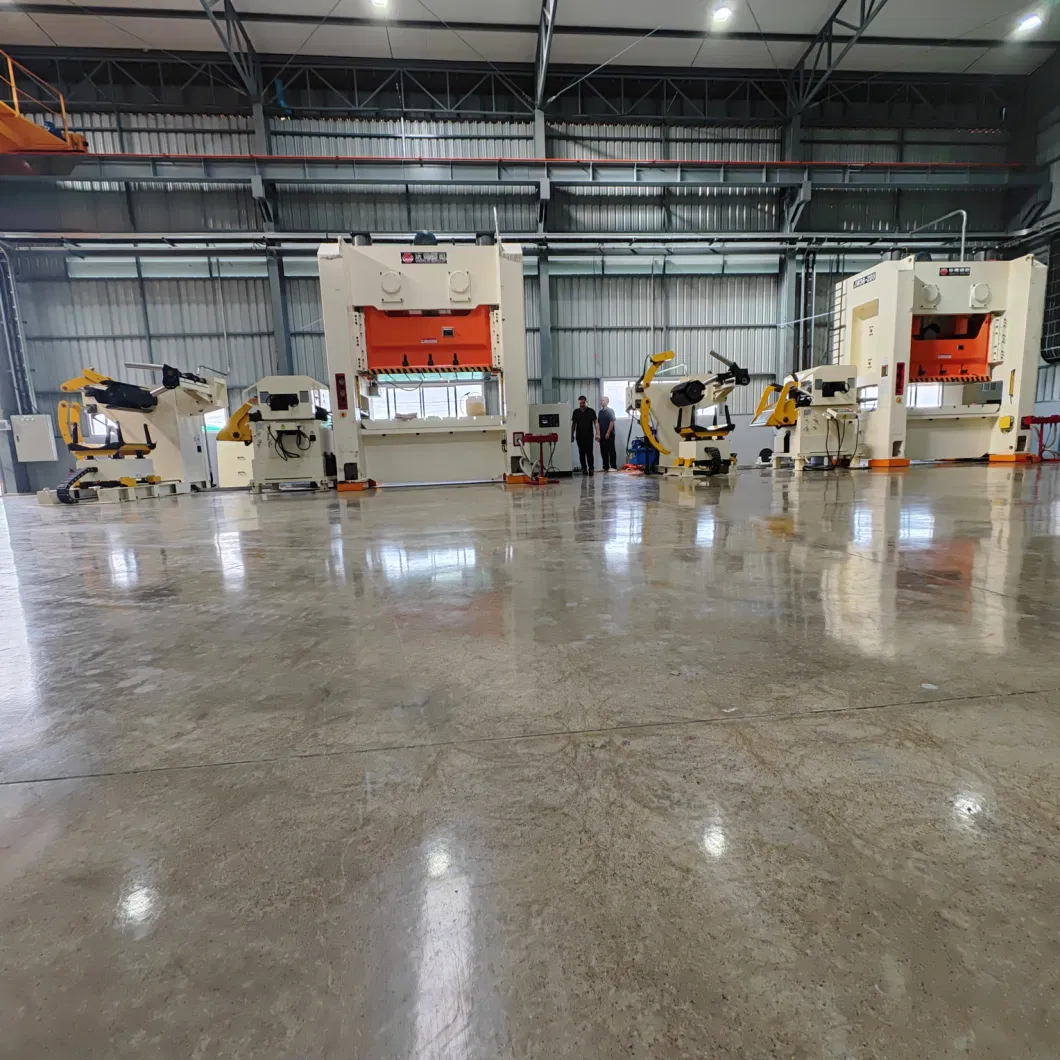
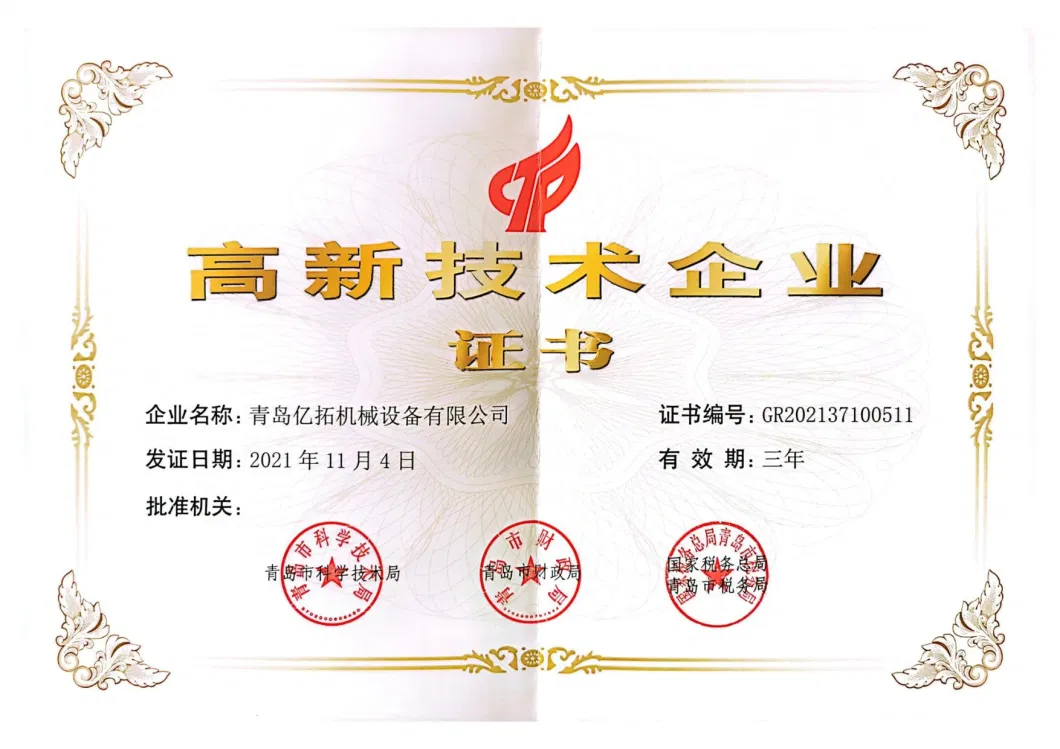
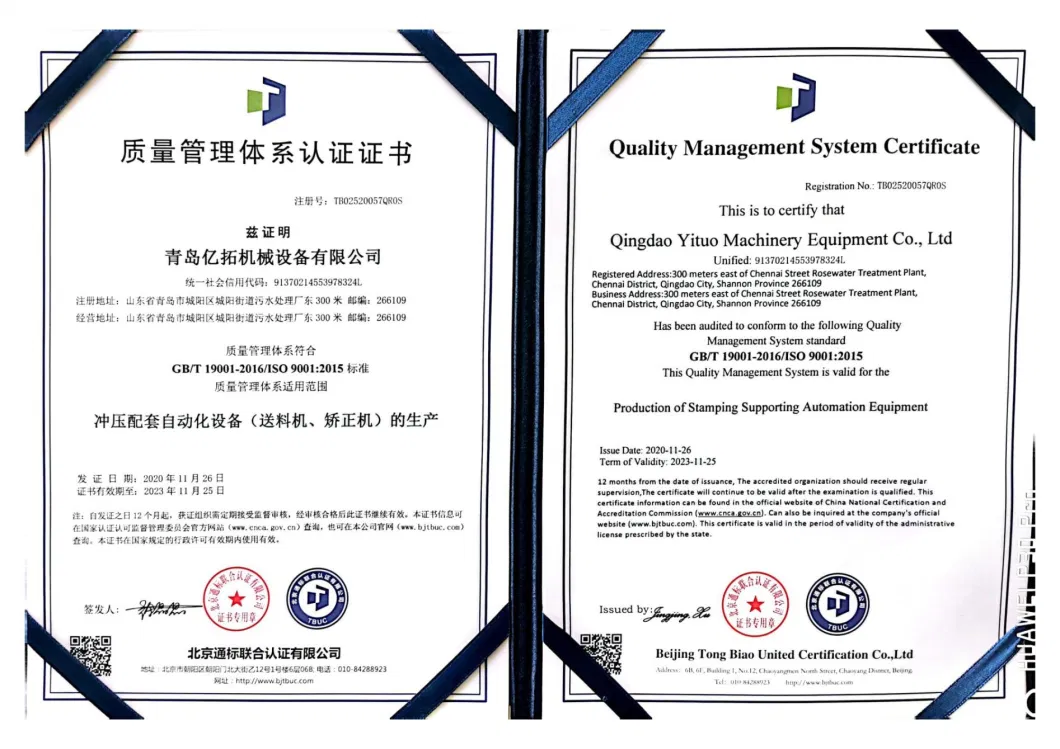
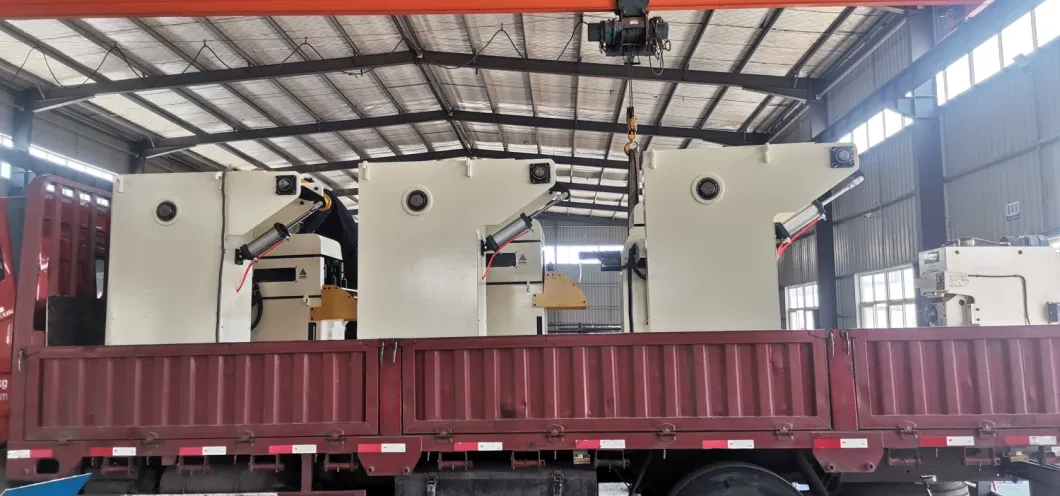
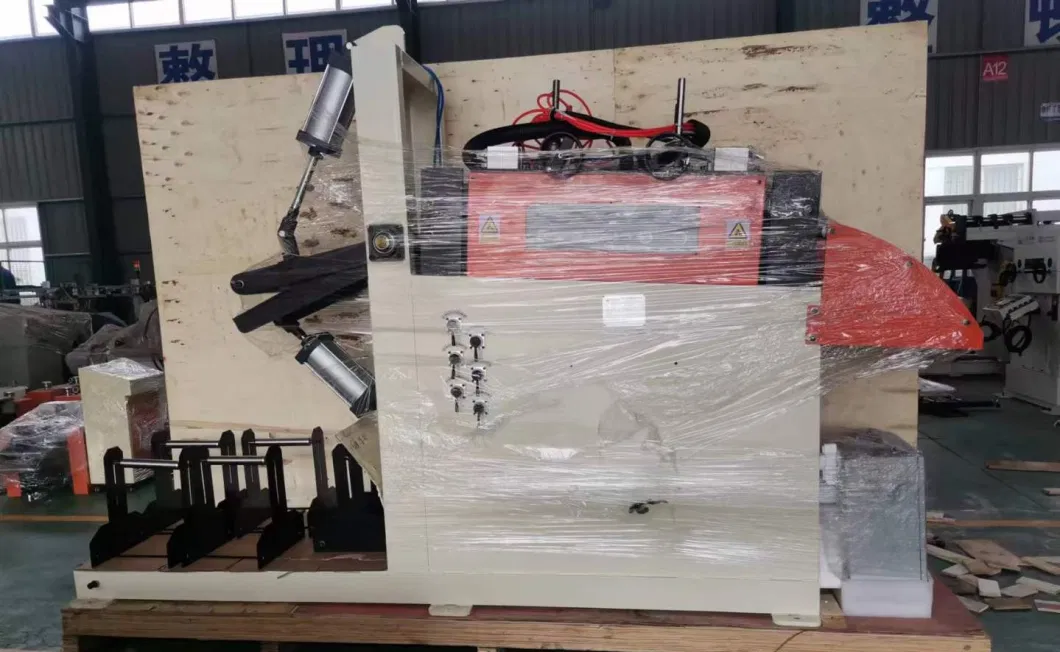
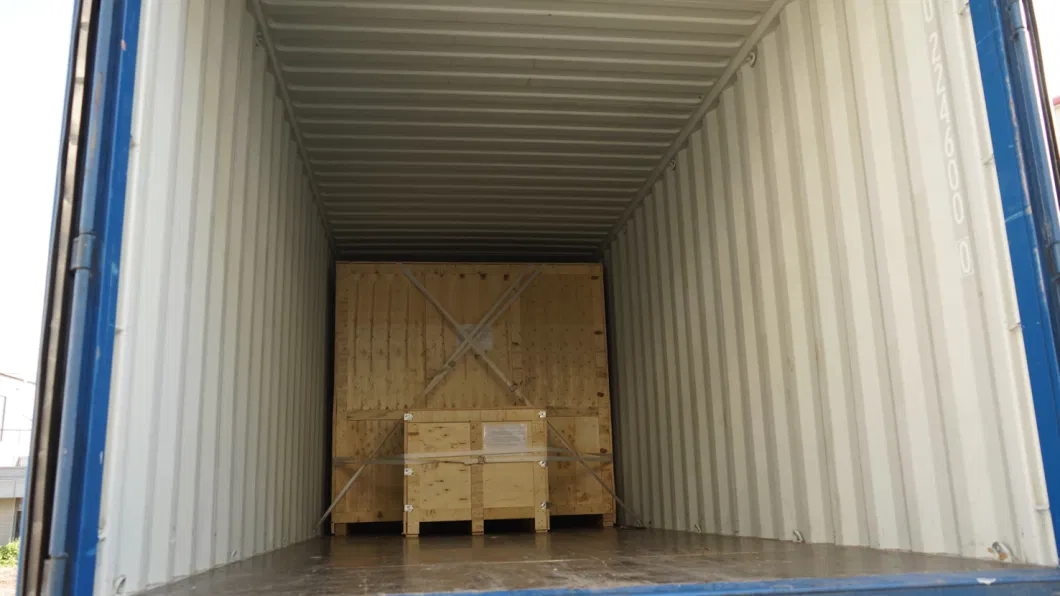
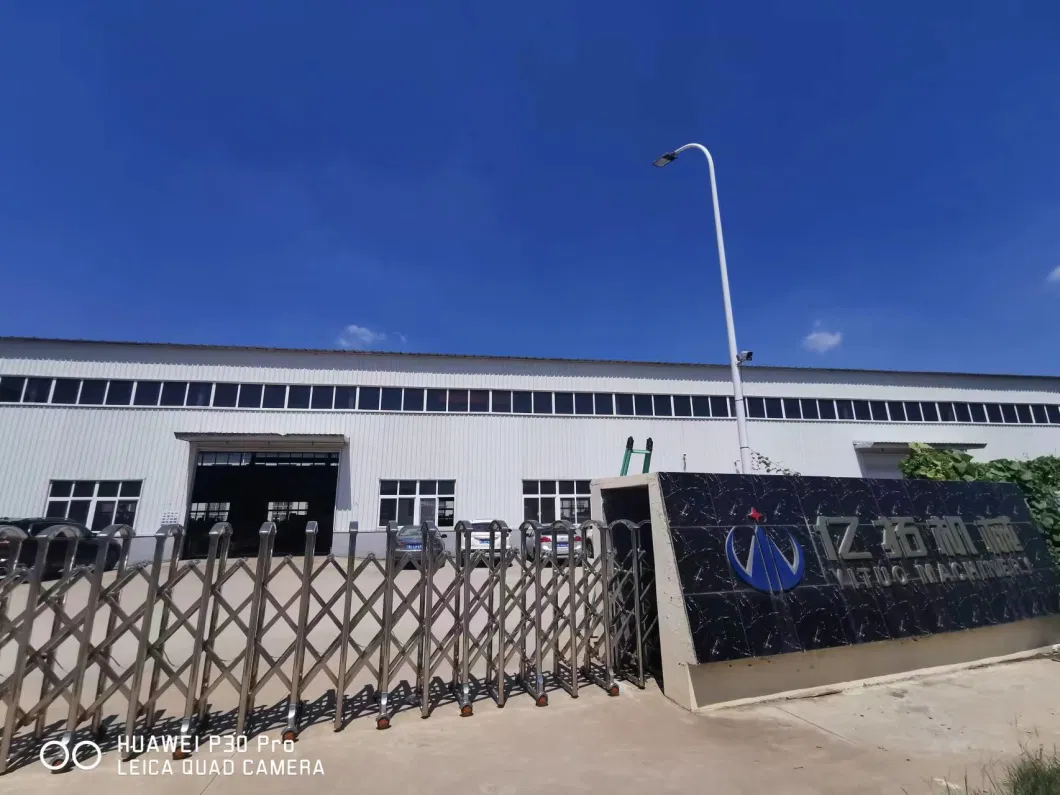
Qingdao Yituo Machinery Equipment Co., Ltd. implements Japanese technology into the production line, and uses a complete and excellent processing system through systematization, special accessories, etc., to flexibly and quickly supply the needs of each machine assembly to ensure product quality and delivery timeliness, Timely service. Strictly follow standard operations to create high-precision and high-quality stamping automation equipment comparable to Japanese models.
Our company adheres to the concept of long-term development and implements the research and development plan. Through the guidance of Japanese technical consultants, based on rich creativity and many years of production technology and practical experience, we have transferred complete key technologies and developed and manufactured first-class technology in the company. With the cooperation of the personnel, a new quality benchmark has been established for the stamping feeder manufacturing industry.
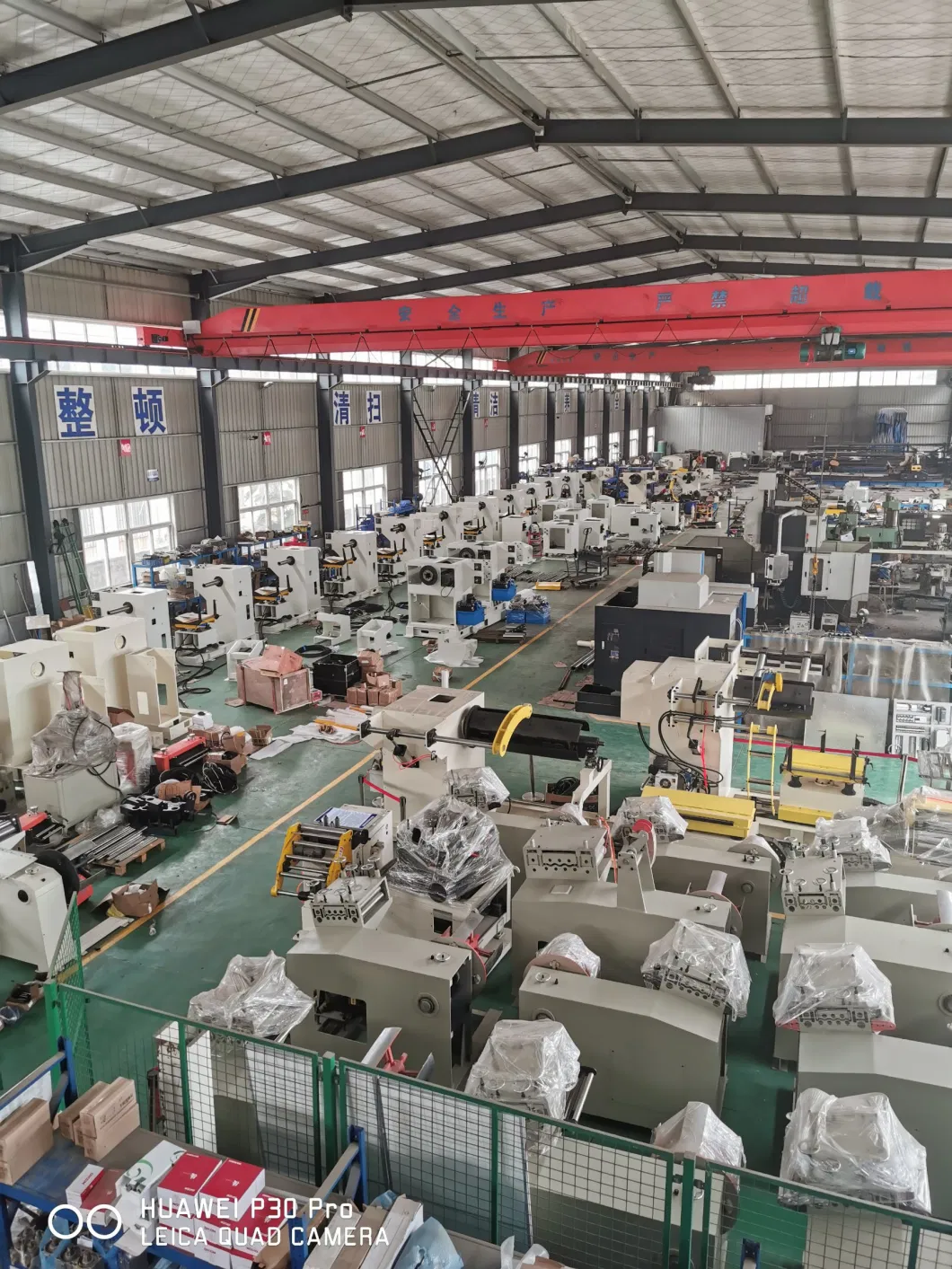
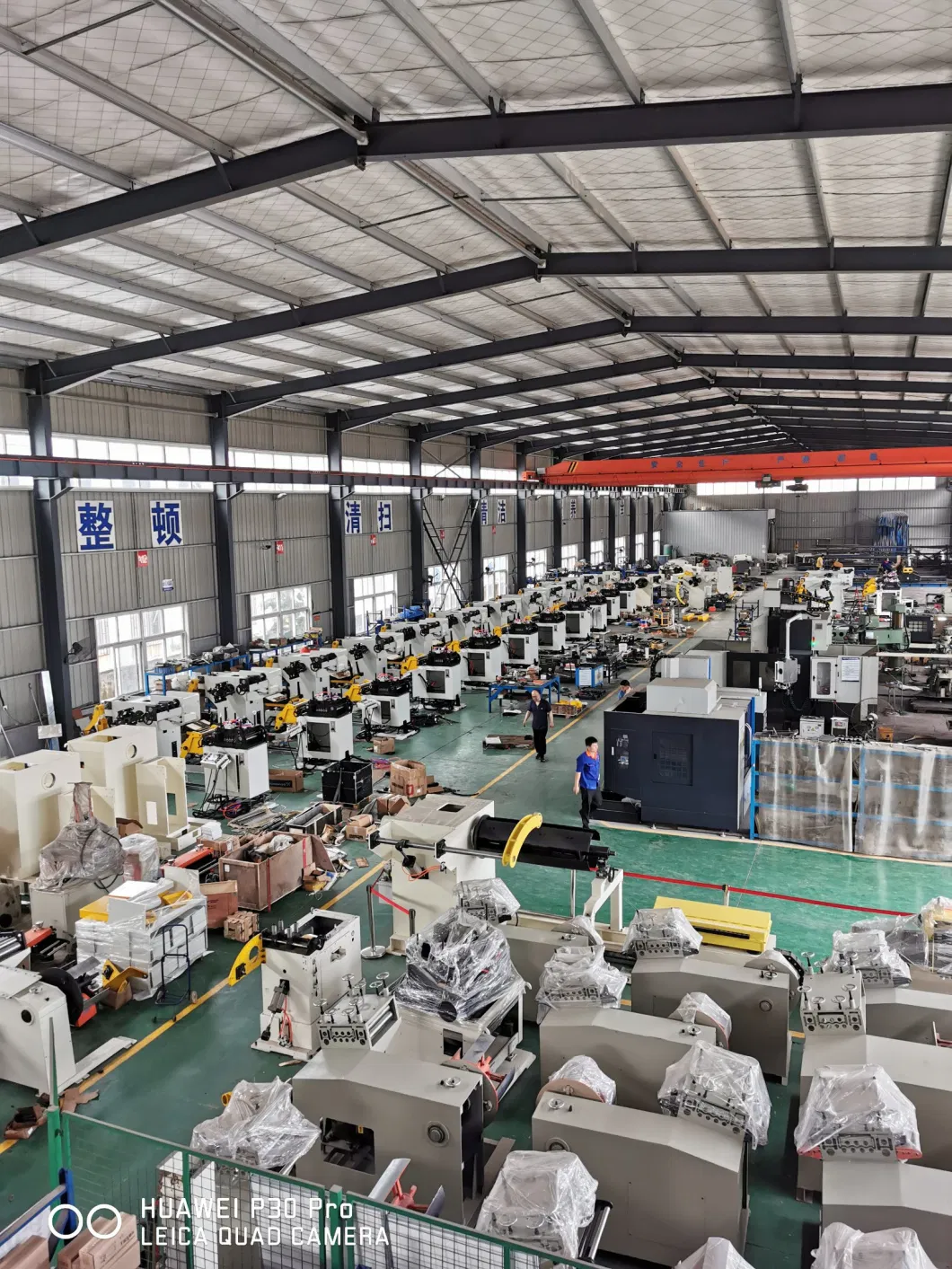
A: We are a factory which has been producing punch press peripheral automatic equipment machines for more than 21 years.
Q: What are your main products?
A: We specialize in manufacturing press machine, decoiler straightener, feeder, metal stamping die, transfer arms, etc.
ie, we mainly help customers contract to build the whole stamping line projects.
Q: What's the delivery time?
A: The standard machine is 25 to 30 days after payment. If asked to supply the whole production line by our customer, we will confirm
the delivery time based on the specific project itself.
Q: What's your payment term?
A: we advise a 30% T/T deposit, balance paid before shipment.
Q: Do you receive OEM?
A: Yes, we warmly welcome customers to do OEM in our factory.