Basic Info.
Model NO.
ND-HF-1250
Transport Package
Steel Sheet
Specification
Custom Design
Trademark
Nianda
Origin
China
HS Code
8514901000
Production Capacity
1-15
Product Description
walking beam reheating furnace features and description of working process:
It is mainly designed for heating of copper, copper alloy in controllable atmosphere before rolling. This production line adopts the most advanced and reliable atmosphere control technique. The whole working procedure can be automatically controlled; It saves investigation cost, with high thermal efficiency, reliable and safety operation.
Installation level and Main Characteristics:
To save energy, reduce heat loss, it adopts one end loading and the other end unloading method, furnace door will need not to be frequently opened during production.
The proper and reliable hydraulic system ensures slab can be evenly and smoothly transferred in side of furnace chamber, no sliding and no scratch; The advanced positioning devices and aligning devices can make sure that slab can exactly positioned and delivered to rolling machine.
High quality imported combustion device and perfect control system ensure temperature can be automatically controlled; The double-cross limit controller ensures air-gas ratio is automatically regulated, and atmosphere inside of furnace chamber is adjusted.
Each heating zone can be individually controlled with help of analyzer and industrial PC. Inner atmosphere can be regulated as micro-reducing atmosphere, neutral atmosphere, and micro-oxidizing atmosphere.
To meet requirement of small batch of workpieces to be suitable to heated in the furnace, working process can be modified or re-set at any time.
The "soften loading" function ensures surface of slab remain in good condition.
To improve surface quality of slab flow rate inside of furnace chamber can be regulated. Burner can be controlled automatically or remote manually controlled.
The "stepping" function ensures slab can be uniformly heated.
Proper history records function.
The working process parameter and temperature curves are recorded and stored in the industrial PC.
Slab numbers will be automatically calculated in the control system.
Alarm history will be stored for operator analyzing and management.
It is mainly designed for heating of copper, copper alloy in controllable atmosphere before rolling. This production line adopts the most advanced and reliable atmosphere control technique. The whole working procedure can be automatically controlled; It saves investigation cost, with high thermal efficiency, reliable and safety operation.
Installation level and Main Characteristics:
To save energy, reduce heat loss, it adopts one end loading and the other end unloading method, furnace door will need not to be frequently opened during production.
The proper and reliable hydraulic system ensures slab can be evenly and smoothly transferred in side of furnace chamber, no sliding and no scratch; The advanced positioning devices and aligning devices can make sure that slab can exactly positioned and delivered to rolling machine.
High quality imported combustion device and perfect control system ensure temperature can be automatically controlled; The double-cross limit controller ensures air-gas ratio is automatically regulated, and atmosphere inside of furnace chamber is adjusted.
Each heating zone can be individually controlled with help of analyzer and industrial PC. Inner atmosphere can be regulated as micro-reducing atmosphere, neutral atmosphere, and micro-oxidizing atmosphere.
To meet requirement of small batch of workpieces to be suitable to heated in the furnace, working process can be modified or re-set at any time.
The "soften loading" function ensures surface of slab remain in good condition.
To improve surface quality of slab flow rate inside of furnace chamber can be regulated. Burner can be controlled automatically or remote manually controlled.
The "stepping" function ensures slab can be uniformly heated.
Proper history records function.
The working process parameter and temperature curves are recorded and stored in the industrial PC.
Slab numbers will be automatically calculated in the control system.
Alarm history will be stored for operator analyzing and management.
No. | Code | Slab Size (mm) | Annual productivity Pieces ( % ) | Annual Productivity (t) | |||
1 | C10100 C10200 | 230×620×8000 | 40 | 120,000 | |||
2 | C11000 | 230×620×8000 | 20 | 60,000 | |||
3 | C19200 | 230×620×8000 | 20 | 60,000 | |||
4 | C19400 | 230×620×8000 | 15 | 45,000 | |||
5 | C70250 | 230×620×8000 | 5 | 15,000 | |||
Total amount | 100 | 300,000 | |||||
Remarks: Copper slab with thickness 170~ 230mm , length 4800 ~ 8000mm can be heated in this walking beam furnace. | |||||||
No. | Item | Technical Data | |||||
1 | Name of equipment | Walking-beam re-heating furnace | |||||
2 | Name of Workpieces | Copper slab and copper alloy slab | |||||
3 | Specification of Copper Slab | 230mm × ( 400 ~ 650 ) mm× 8000mm ; 230mm × ( 400 ~ 650 ) mm× 4800mm ; 210mm × ( 400 ~ 650 ) mm× 7200mm ( 230mm × 620mm × 6600mm ) | |||||
4 | Production Rate | Maximum:60t/h 6pieces/h | |||||
5 | Slab Temperature | 800 ~ 1050 ± 5 | |||||
6 | Temperature of Furnace Chamber | Maximum 1150 | |||||
7 | Fuel | City Gas | |||||
8 | Calorific Volume | 3500 ~ 3800Kcal/Nm 3 | |||||
9 | Calculated Calorific Volume | 3600Kcal/Nm 3 | |||||
10 | Pre-heated air temperature | 250 -400 ( during normal working time ) | |||||
11 | Thermal efficiency | ≥60% | |||||
12 | Thermal Control Method | Burner flame is remote, automatic, and continuously controlled. | |||||
13 | Burner Type | Flat Flame Burner + Long Flame Burner | |||||
14 | Burner Numbers | Total 55 pieces , heating section : 35pieces , soaking section 20 pieces. | |||||
15 | Rated Combustion rate | Maximum : 6000 Nm 3 /h | |||||
16 | Chamber Dimension | Width 9000× Height 1100(600)× Length 16800mm | |||||
17 | Loading capacity | Slab quantity: 21pcs/batch×10t/piece=210t/ batch | |||||
18 | Total Length of furnace body | About 27.6meters | |||||
18 | Feeding & discharging method | Side feeding and side discharging | |||||
19 | Loading Method | Single Row, centralized in middle position | |||||
20 | Stroke distance of Movable beam | Upward move: 90mm , Downward move: 80mm | |||||
21 | Horizontal moving distance of movable beam | 800mm or 400mm ×2 ( it shall be negotiated with buyer ) | |||||
22 | Heat Exchanger Model | Tube type ( direct cross and counter current ) | |||||
23 | Heating Time | About 3.5 hours | |||||
24 | Temperature control Zones | 9 zones |
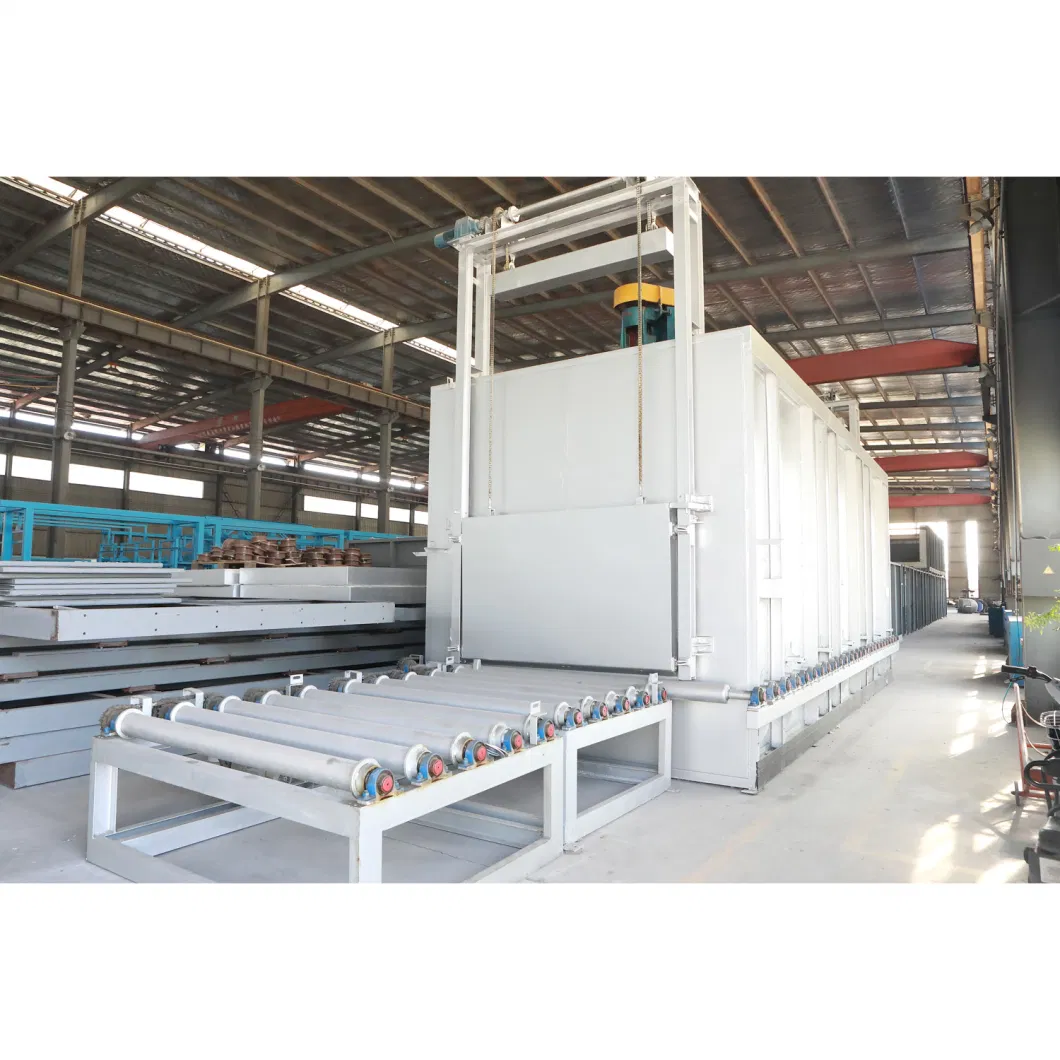
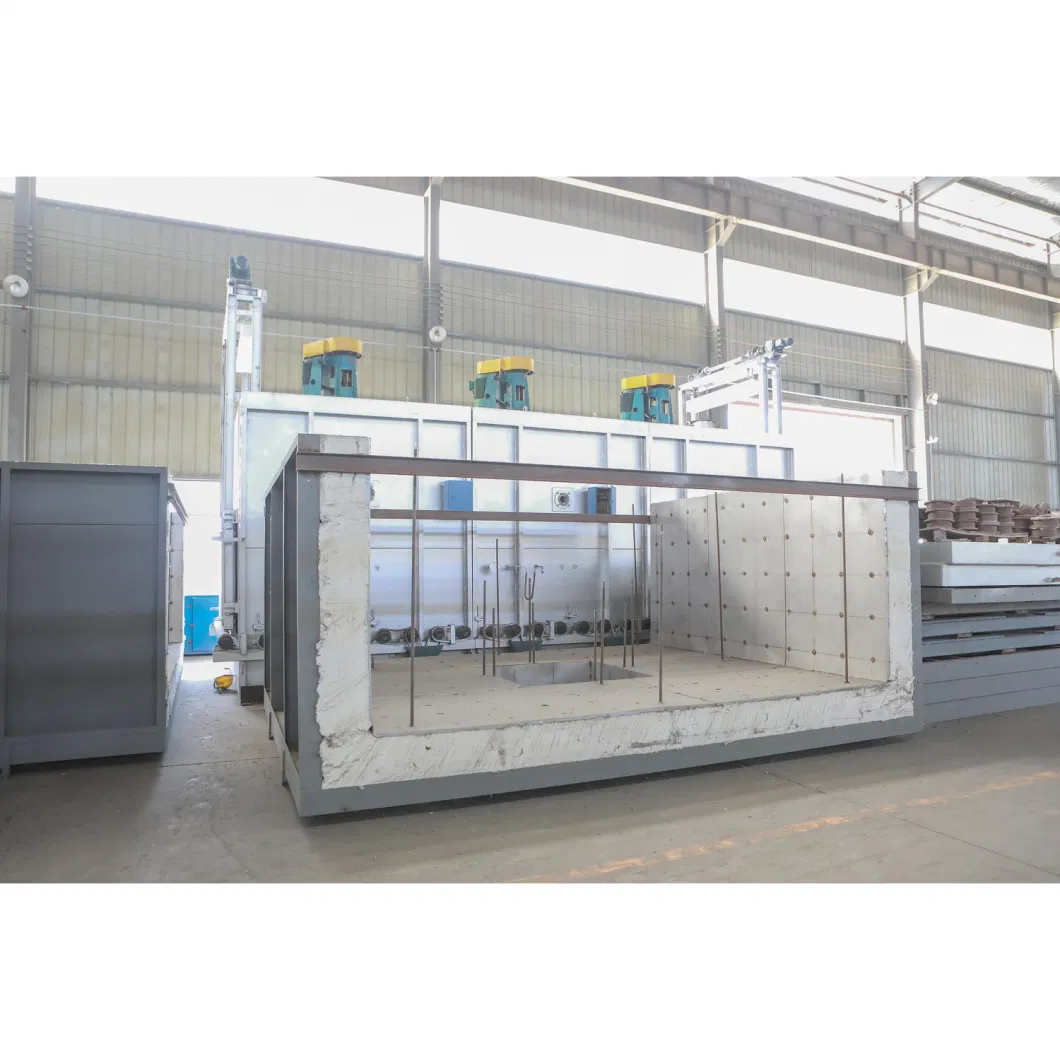
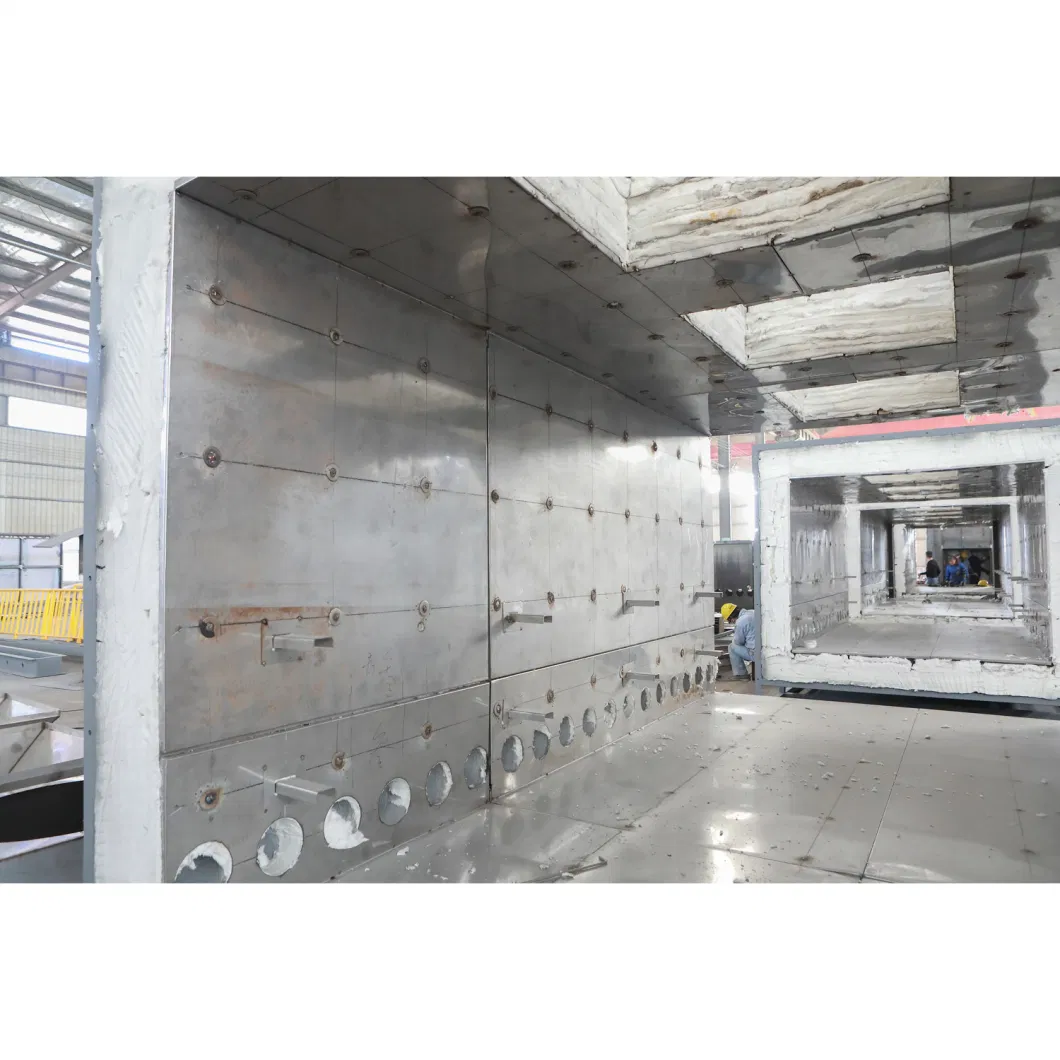
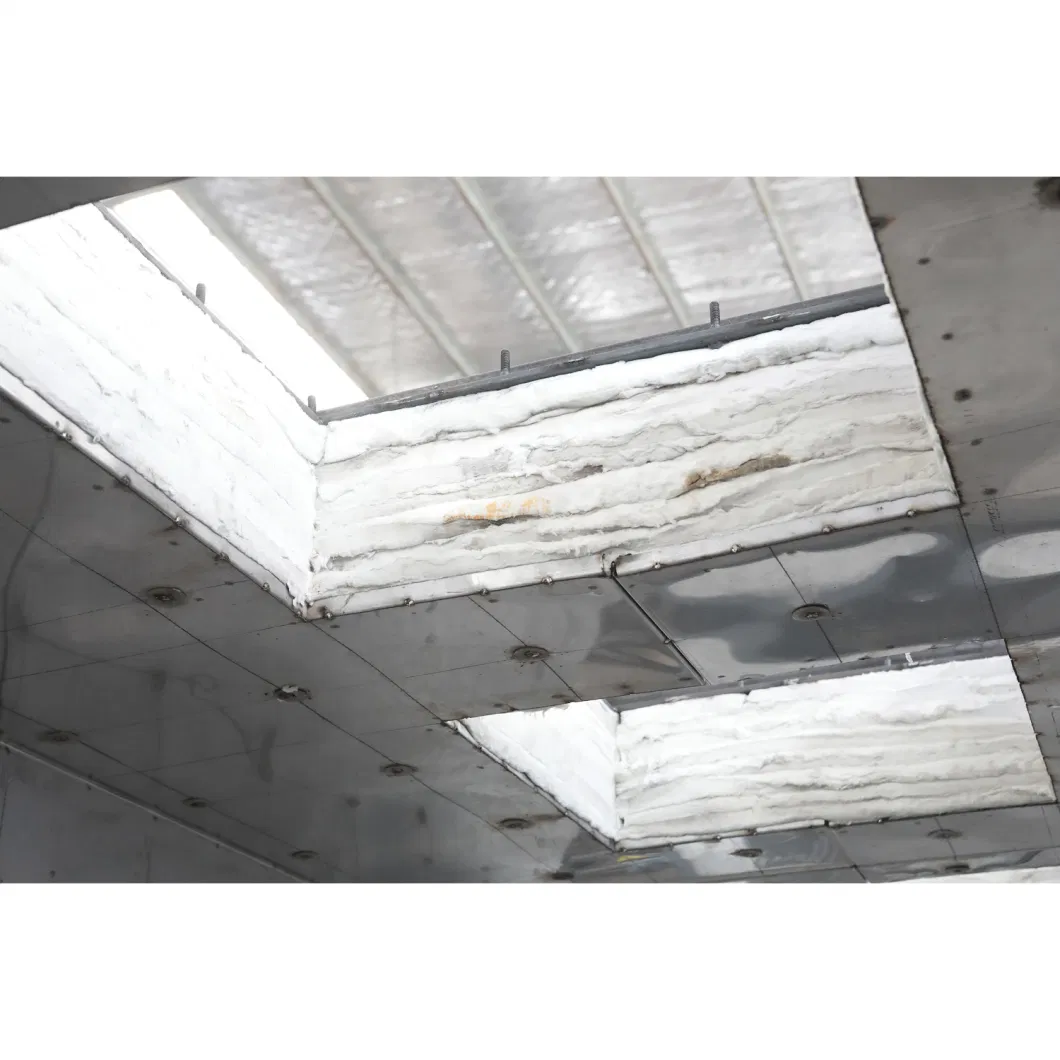
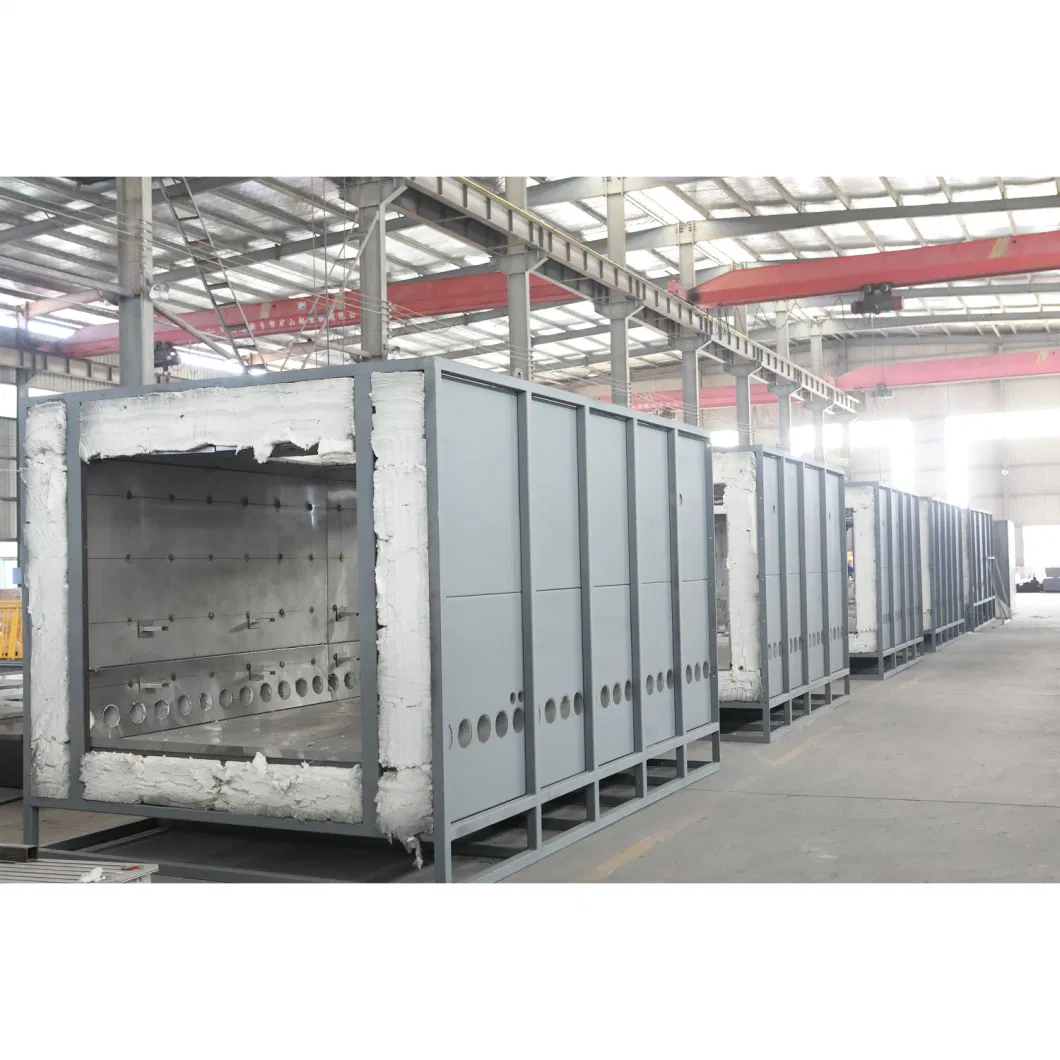
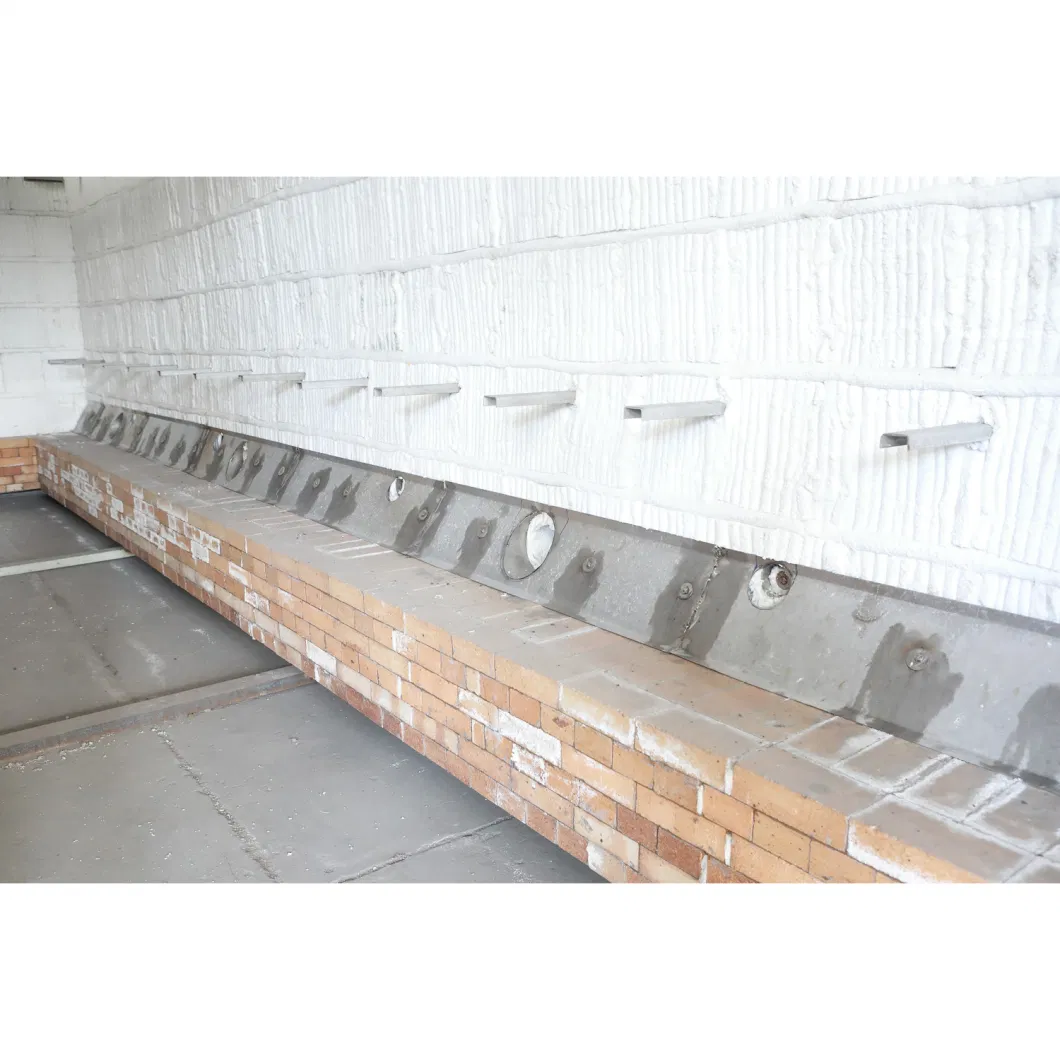
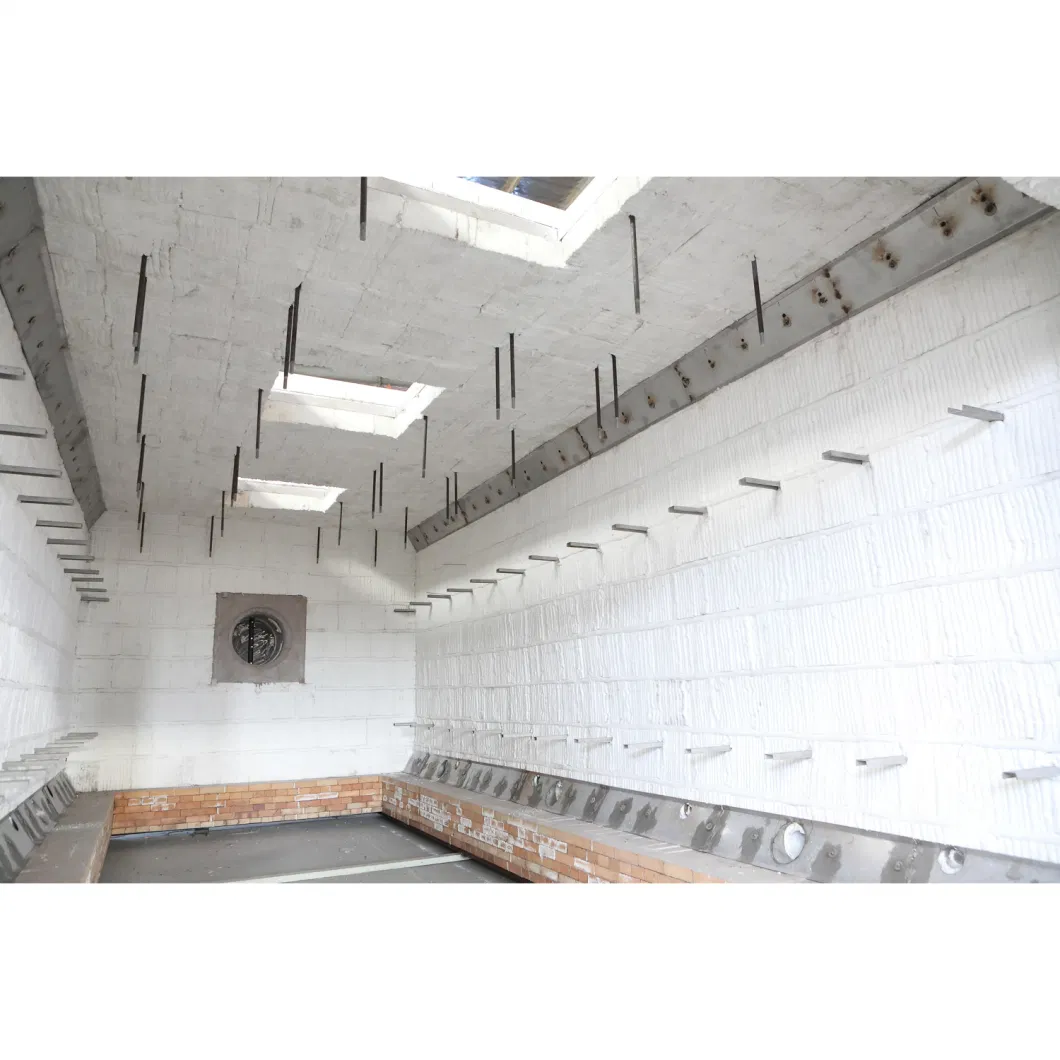
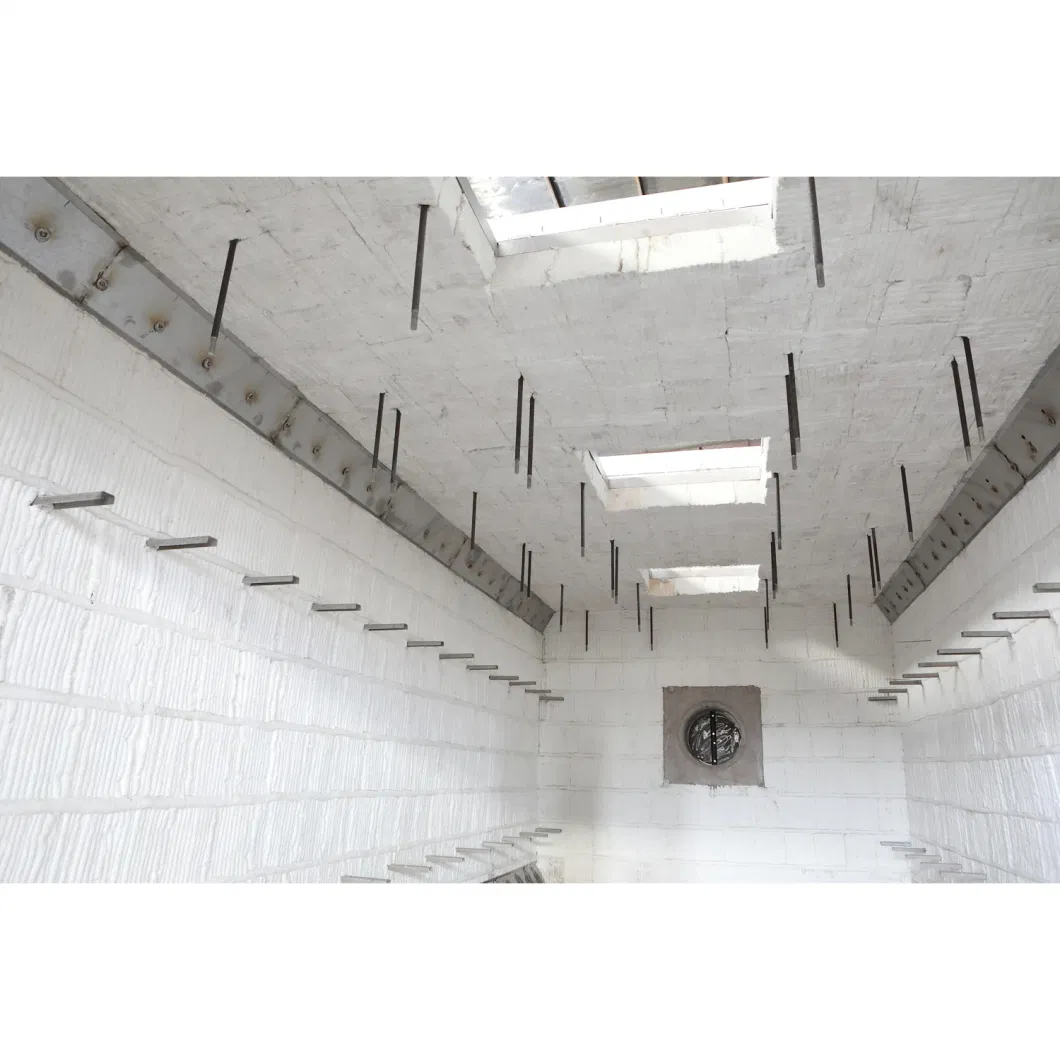
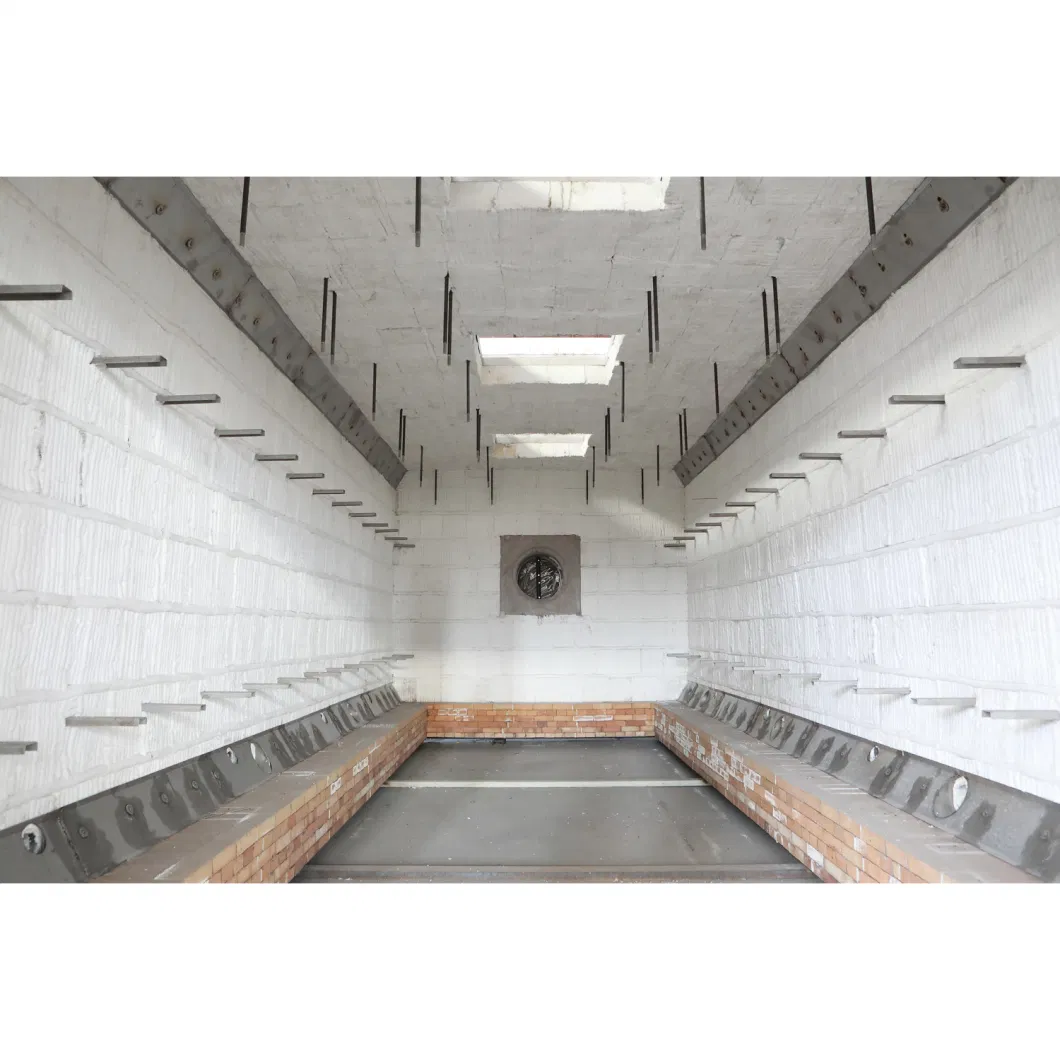
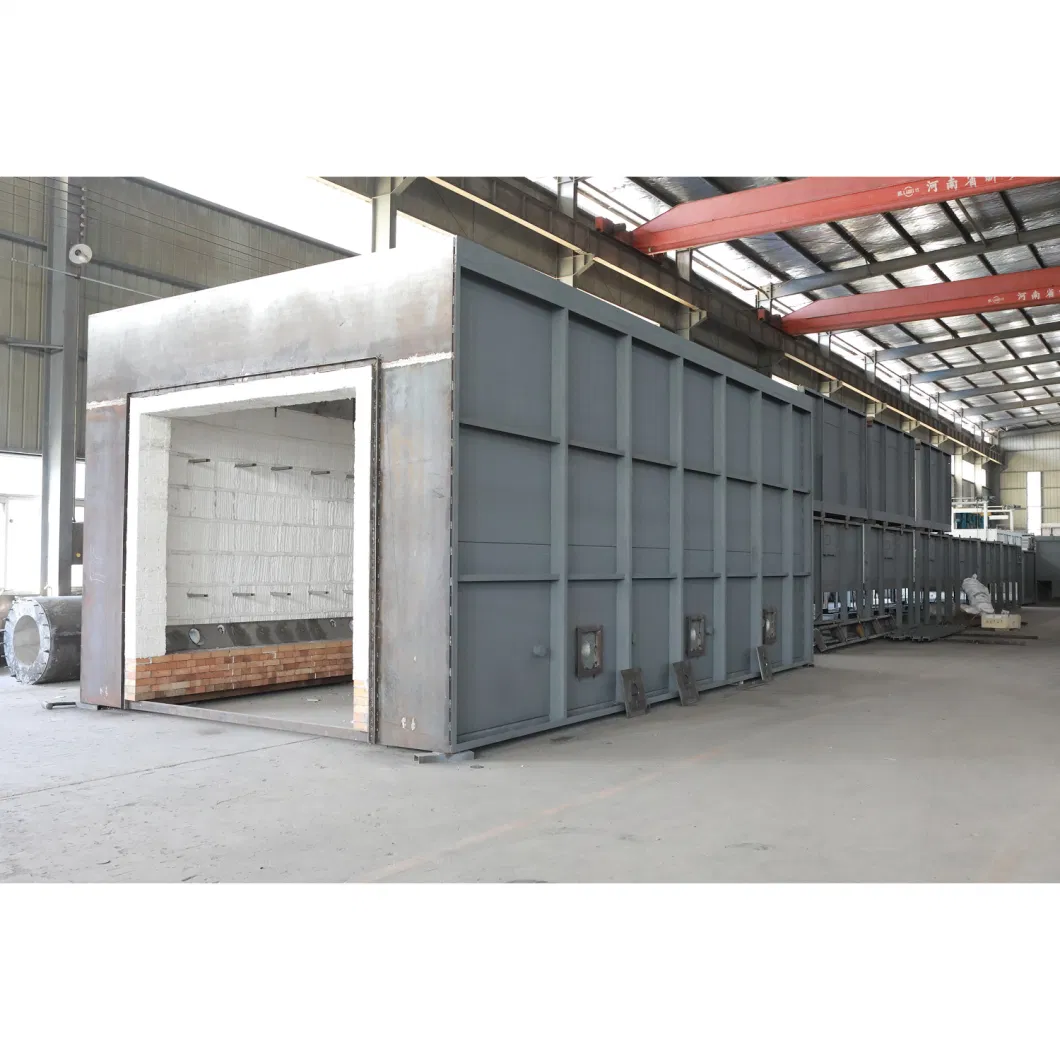
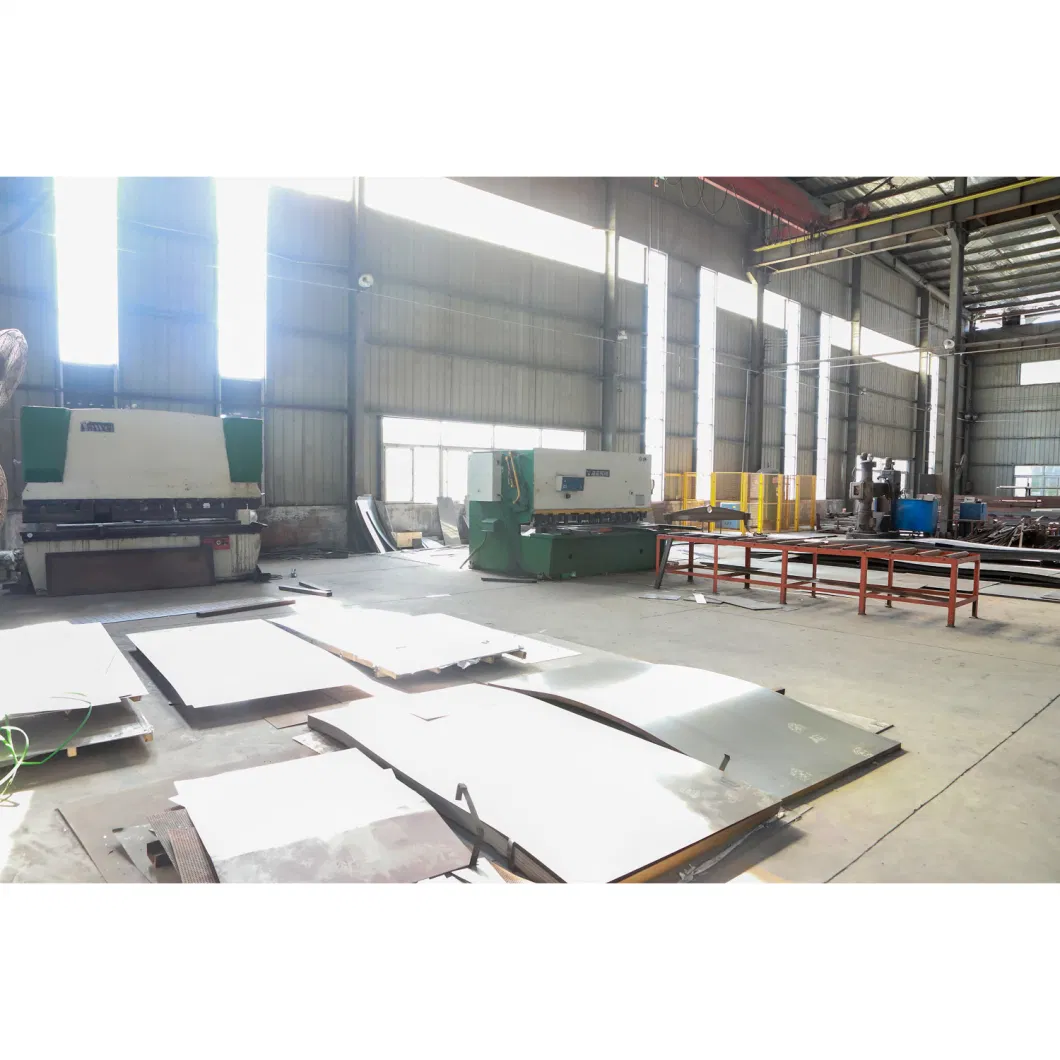
Main technical parameter of feeding table: |
No. | Item | Parameter |
Small walking beam feeding table | ||
1 | Overall Size | 7830×6000 |
2 | Working Height | 800mm |
3 | Fixed Frame Beam | 5 pieces |
4 | Movable Frame Beam | 4 pieces |
5 | Feeding Width of Over-head Crane | 900mm |
6 | Maximum Lifting Height of Movable Beam | 300mm |
7 | Maximum Horizontal Moving Distance | 800mm |
8 | Motor Power of Hydraulic Pump | 18.5Kw×(1+1) |
9 | Motor Power of Circulating Pump | 5.5Kw |
10 | Horizontal Moving Cylinder | φ100 -450mm |
11 | Lifting Cylinder | φ140 -950mm |
Alignment Device (Centralizing Device ) | ||
12 | Cylinder Number | 2 pieces |
13 | Cylinder Specification | QGB-160×400 |
14 | Working Pressure | 0.5 ~ 0.7MPa |
Measurement Roller Table | ||
15 | Length of Roller Table | 8330mm |
16 | Width of Roller Table (length of motor is not included) | 1080mm |
17 | Working Height | 1000mm |
18 | Driving Roller Number | 8 Pieces |
19 | Driven Roller number | 9 pieces |
20 | Motor Power of Roller Conveyor | 2.2Kw |
Front Roller Table | ||
21 | Length of Roller Table | 1830mm |
22 | Width of Roller Table (Motor length is not included | 1080mm |
23 | Working Height | 1000mm |
24 | Driving Roller Number | 2 |
25 | Driven Roller Number | 2 |
26 | Motor Power of Roller Conveyor | 2.2Kw |