- Overview
- Product Description
- Detailed Photos
- Packaging & Shipping
- Our Advantages
Basic Info.
Product Description
3 in 1 combination metal coil processing machine decoiler straightener and servo feeder large blanking production line
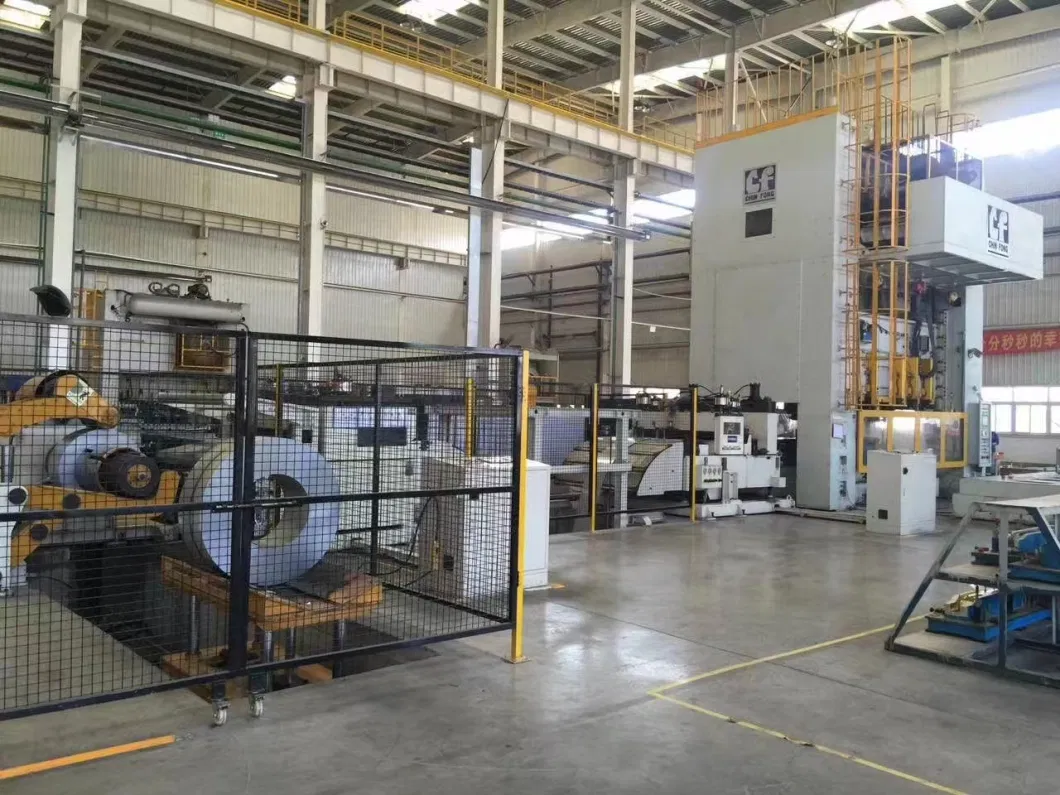
STANDARD ACCESSORY
1. Electric eye loop control system
2. Outgoing catenary to assist and support the material
3. Feed and Straightener rolls with a hard chrome finished
4. Feeding line easily adjusts by advance worm gear screw jacks device
5. Straightener adjusts by advance worm gear screw jacks device
6. Left/right swing tension roll support device
7. Reference indicator adjsuter
8. Coil material entry support assembly
9. Straightener opener device
10. Hold down arm device
11. A cluster gear set maximizes transmission of horsepower
12. Transformer
13. PLC Control Feeding program from mitusbishi
OPTION
1. Coil car
2. Shearing machine
Function instruction: use the unbending principle to release material bending stress to straighten the plate, then feed into the press
equipment according to set length and speed.
Driven method: AC servo motor
Straightening-feeding roller combination: straightening roller; assistant roller; feeding roller.
Straightening measure display method: dial display.
Straightening roller release method: pneumatic release.
Straightening measure adjusting method: manually wheel (Electrically Adjust for optional)
Straightening measure adjusting method: electrically adjust (for optional), no need to rotate the hand wheel, more precise, with
date storing function to store each group of material of straightening adjustment date which can save time for future use,
convenient for operation.
Roller driven method: gear driving, all gears adopt tempering, carburization, high-frequency quenching, precise grinding gear
IT6 level precise standard.
Straightening-feeding rollers flip-up system (optional): upper straightening-feeding rollers can be lifted by a hydraulic
cylinder from one side, lifting angle can reach up to 30 degrees. Operating the touch screen HMI or button of the hand operating
box to open the straightening-feeding rollers, this way, easy to clean rollers, to ensure material surface flatness and cleanliness. Adopts double oil cylinder to control.
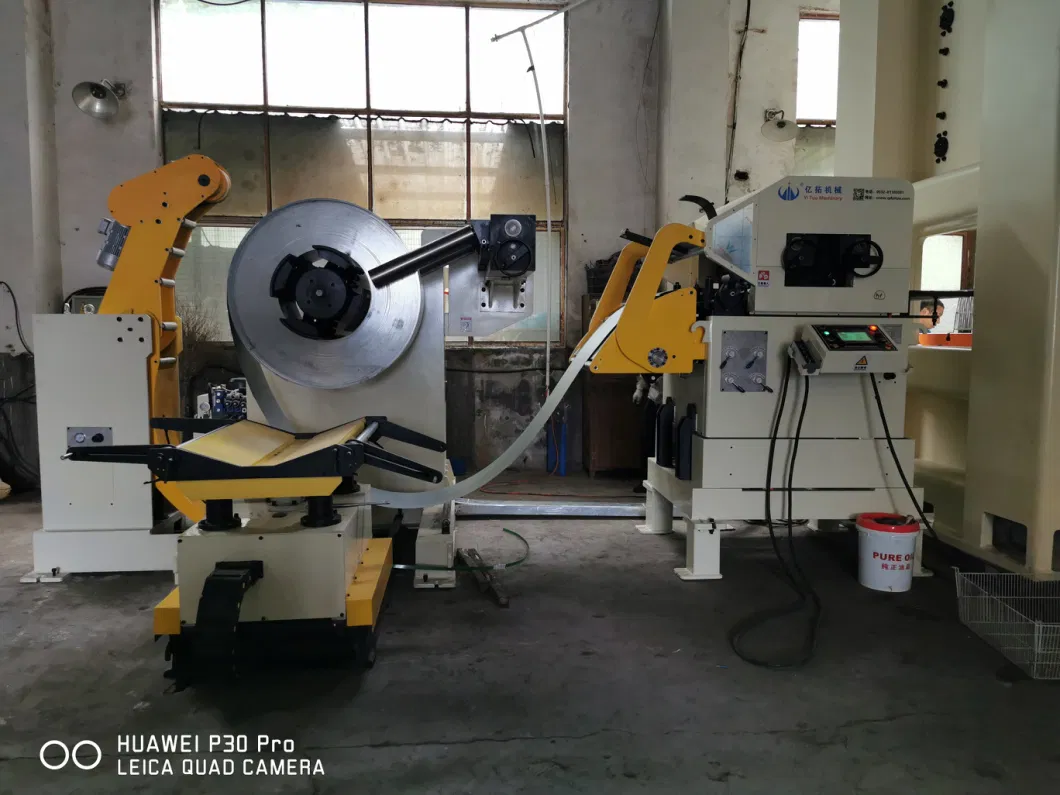
Width of the material | 70mm~600mm |
Thickness of the material | 2.0mm~8.0mm |
Inside coil diameter | Φ460mm~Φ530mm |
Max.coil outside diameter | Φ1600mm |
Max.coil weight | 5 ton |
Straightening roll diameter | Φ120mm×7(upper*4/lower*3) |
Material of straightening roll | GCr15(HRC58-62) |
Feeding roll diameter | Φ136mm |
Decoiler power | 5.5Kw |
Straightening power | 11Kw |
Feeding speed | 0~20m/min |
Feed Pitch accuracy | <±0.2mm |
Other configuration | |
Straightening adjustment type | Eccentric shaft adjusted by worm and gear |
Load material type | coil car |
Feeding line adjust | Electric |
Hold down the arm device | By pneumatic |
Auto threading table device | By hydraulic |
The coil keeper adjusts the width | Manual |
Front coil keeper adjusts open | Pneumatic |
The coil width guide at the straightener | Two hand-wheel adjusted |
Coil tip de-bender device | Hydraulic |
Operation control mode | Main control cabinet + action unit remote control switch |
The coil end detects the sensor | With |
Other technical data | |
Operating air | 0.5Mpa |
Operating hydraulic | 7Mpa |
voltage | 3phase 380V |
Feed Level from floor | 1100mm-1300mm |
Input material type | From down to up |
Delivery side | From left to right |
Equipment length(Not including outlet shelf) | ≈5.0m |
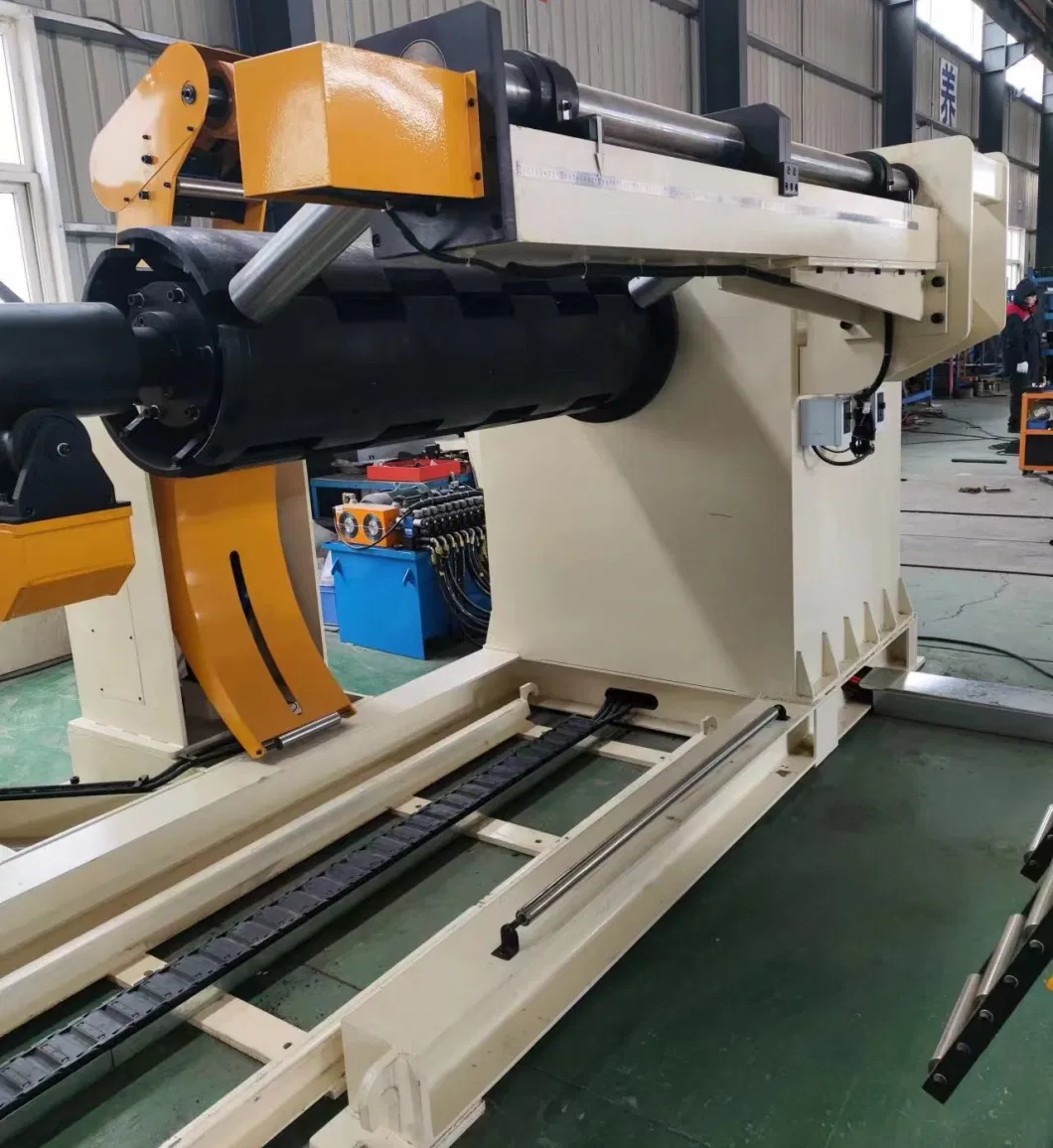
Mandrel of uncoiler
Four pieces of plates.
Each plate is fixed by screws very well.
Cantilever type.
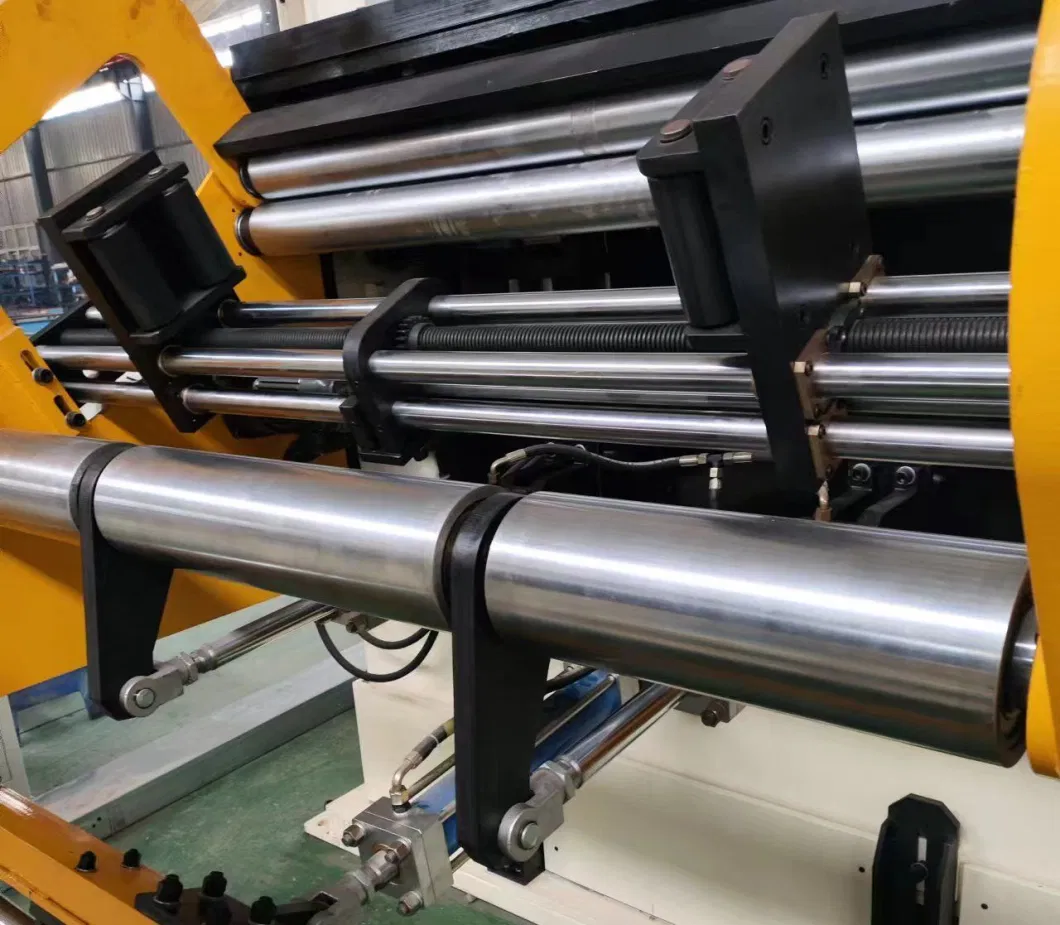
Guiding device for straightener and feeder
While uncoiler decoil coil material, so material can get into the entrance of the feeder easily.
Round mandrel of uncoiler
Automatic expansion, by hydraulic cylinder drive.
Full round, for better loading.
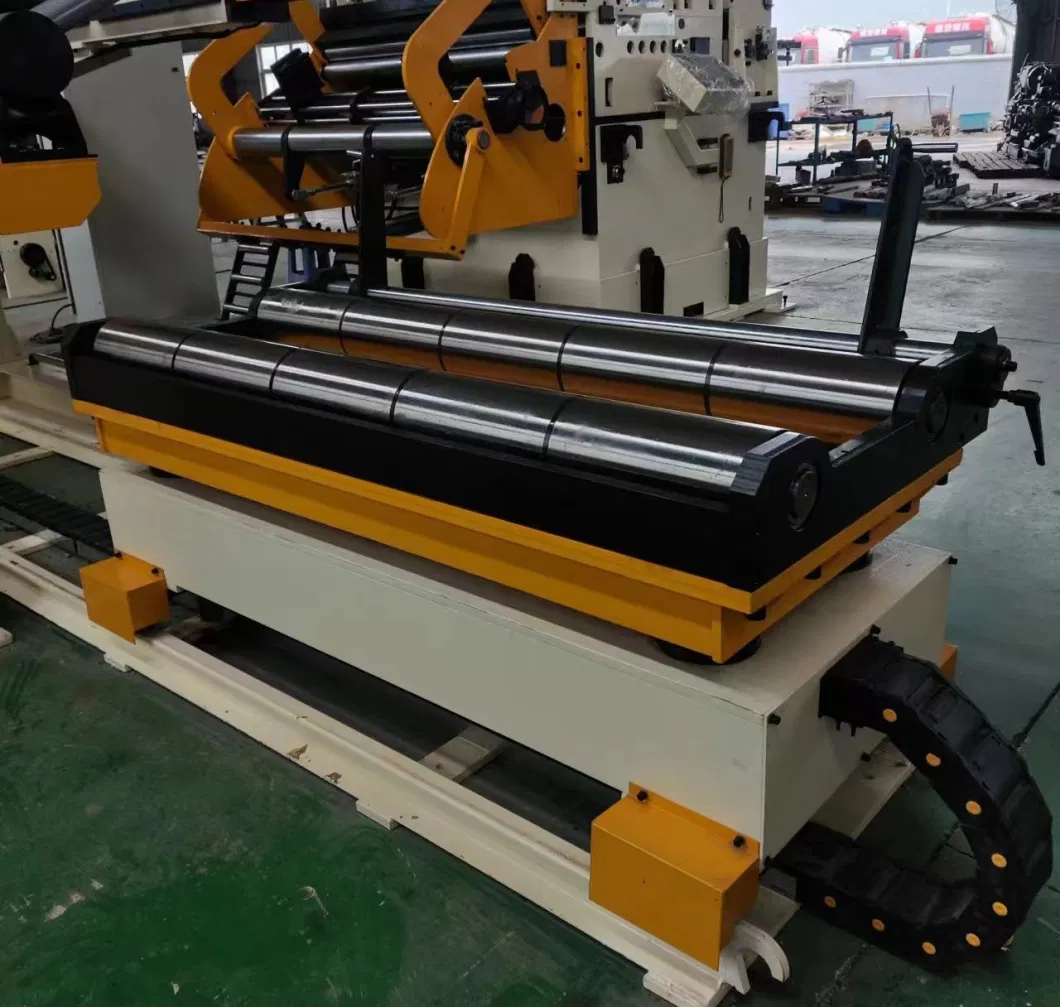
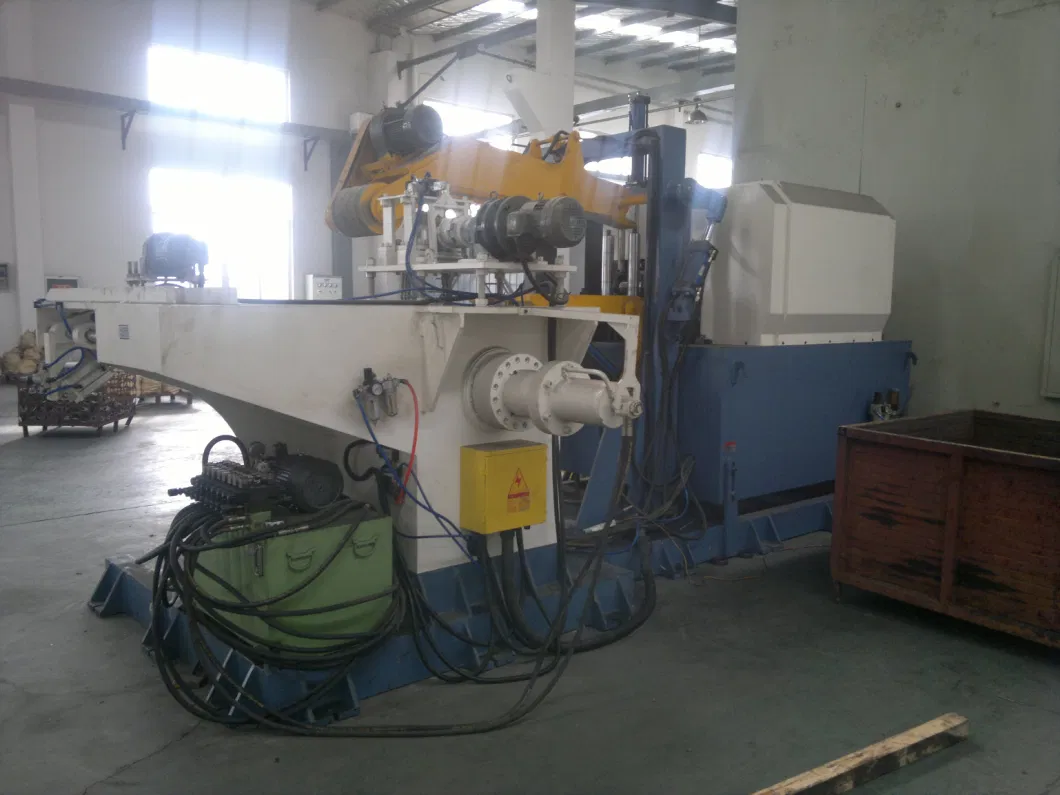
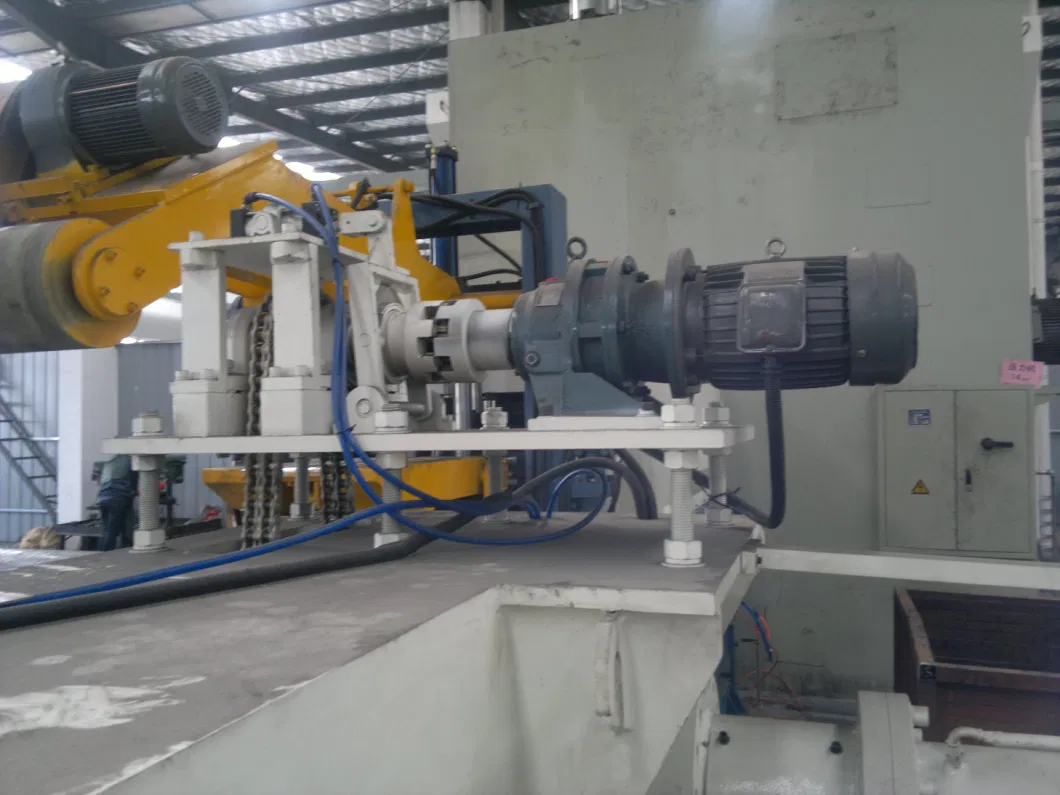
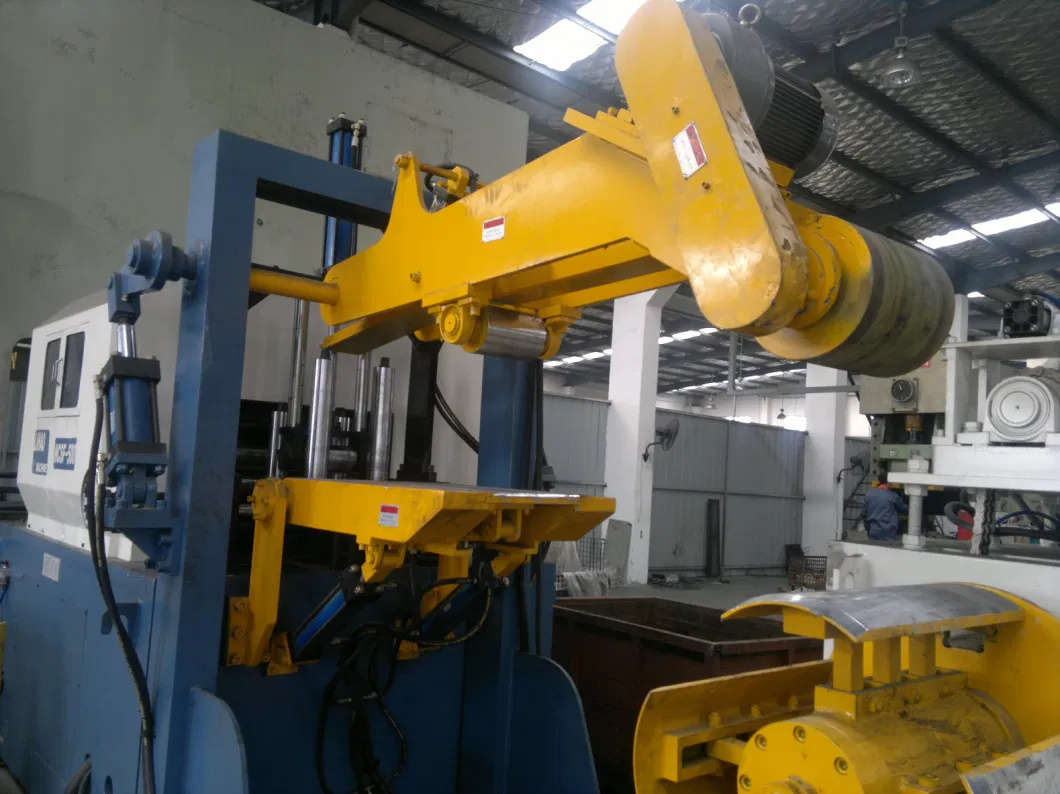
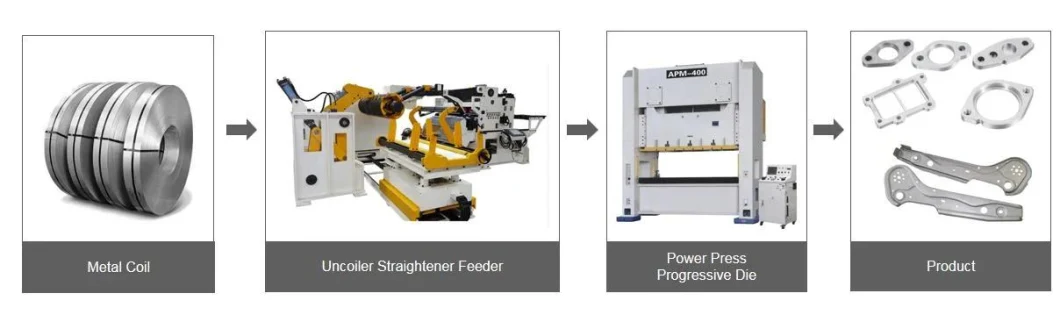
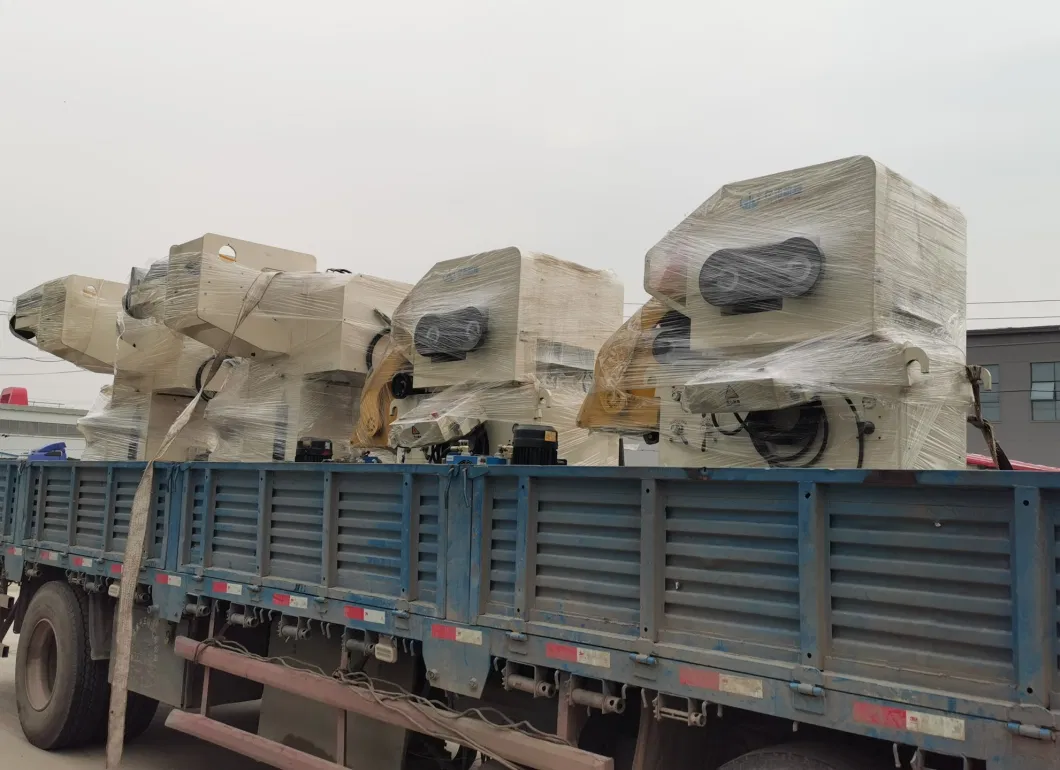
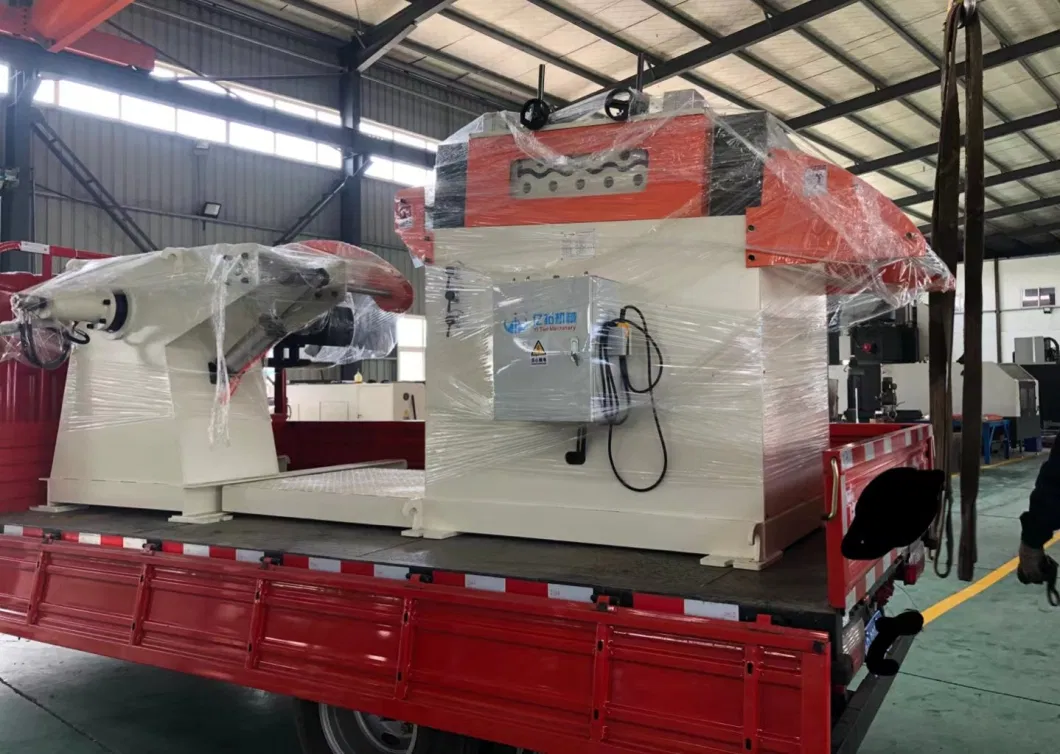
Our company adheres to the concept of long-term development and implements the research and development plan. Through the guidance of Japanese technical consultants, based on rich creativity and many years of production technology and practical experience, we have transferred complete key technologies and developed and manufactured first-class technology in the company. With the cooperation of the personnel, a new quality benchmark has been established for the stamping feeder manufacturing industry.
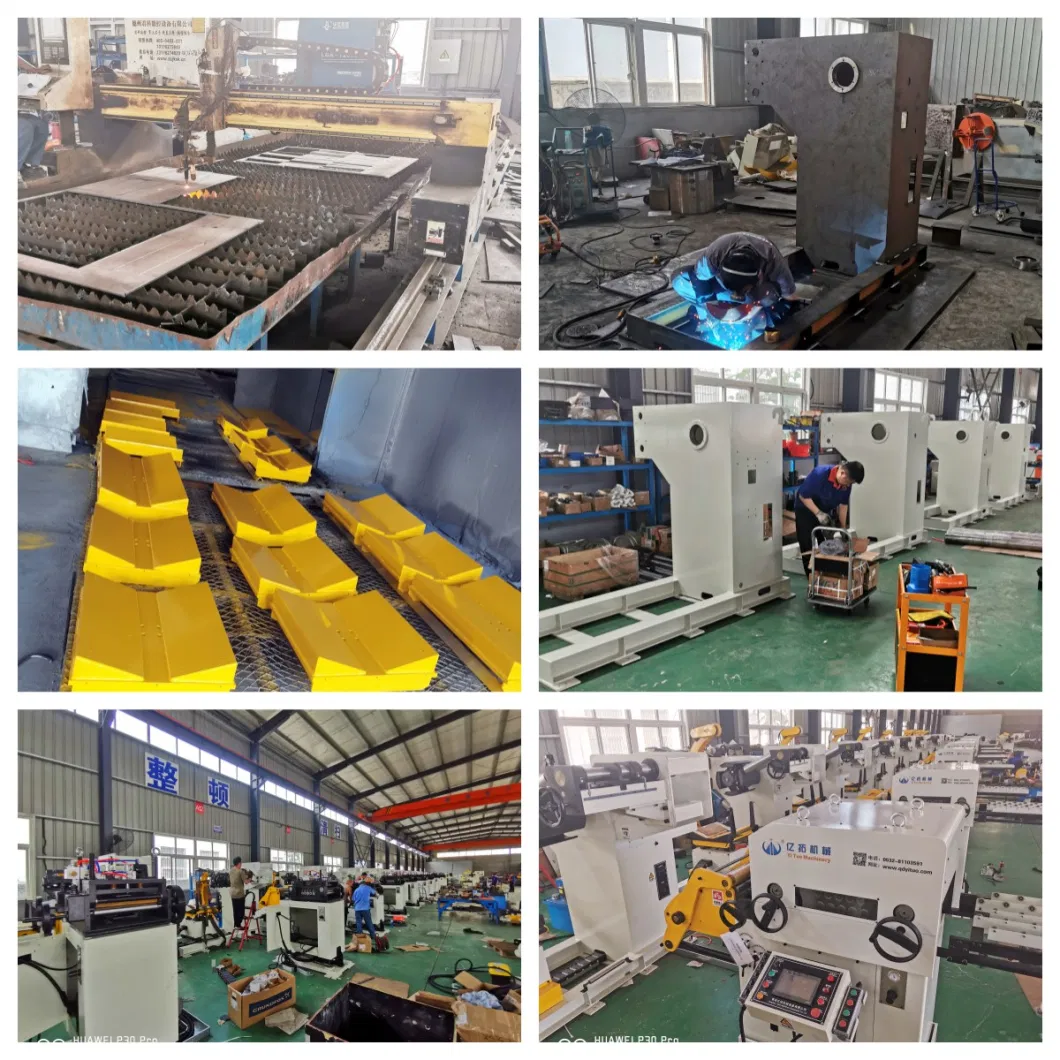